Catalytic cracking method and equipment for hydrocarbon oil
A catalytic cracking and hydrocarbon oil technology, which is applied in the field of hydrocarbon oil catalytic cracking and hydrocarbon oil catalytic cracking equipment, can solve the problems of weakened catalytic effect, increased olefin content in gasoline, and increased thermal cracking reactions, so as to increase the ratio of catalyst to oil and reduce the contact The effect of temperature
- Summary
- Abstract
- Description
- Claims
- Application Information
AI Technical Summary
Problems solved by technology
Method used
Image
Examples
Embodiment approach
[0036] According to one embodiment of the present invention, the method also includes adding hydrocarbon oil to the second reactor, and making the added hydrocarbon oil and the oil gas after the separation of the first oil agent and the newly added second cracking catalyst carry out the described In the second contact reaction, the hydrocarbon oil is one or more of the hydrocarbon oil feedstock, dry gas, liquefied gas, light hydrocarbons, gasoline, diesel oil, recycled oil, and oil slurry.
[0037] The mixture of the oil gas and the catalyst after the second contact reaction is subjected to the second oil agent separation, and the catalyst after the second oil agent separation is stripped to obtain the raw catalyst. The above-mentioned first oil agent separation method can also be used.
[0038] In the present invention, in the second reactor, the regenerated catalyst is used to replace the catalyst that has lost most of its activity in the first reactor, which is beneficial to...
Embodiment 1-3
[0076] This example is used to illustrate the hydrocarbon oil catalytic cracking equipment and hydrocarbon oil catalytic cracking method provided by the present invention.
[0077] use figure 1 The hydrocarbon oil catalytic cracking equipment shown has a processing capacity of 2kg / h, the first reactor and the second reactor are both riser reactors, and the height ratio of the first reactor 2 and the second reactor 5 is 1:1.5 , the diameter ratio is 1:1. The stripping medium is steam at a temperature of 250°C. The catalysts used in the first reactor 2 and the second reactor 5 are MLC-500 balancer. This embodiment is for the purpose of producing more light oil (gasoline+diesel oil), the temperature of the second reactor 5 is lower than the temperature of the first reactor 2, and the oil agent contact time of the second reactor 5 is higher than that of the first reactor 2 Oil contact time, reaction conditions and results are shown in Table 3.
Embodiment 4-6
[0083] This example is used to illustrate the hydrocarbon oil catalytic cracking equipment and hydrocarbon oil catalytic cracking method provided by the present invention.
[0084] The catalytic cracking of hydrocarbon oil was carried out according to the method of Example 1, the difference was that the feed oil was feed oil B, and the catalysts in the first reactor and the second reactor were both MMC-2 catalysts. This embodiment aims at producing more light olefins, the temperature of the second reactor 5 is higher than the temperature of the first reactor 2, and the reaction conditions of the second reactor 5 are more severe than the first reactor 2, reaction conditions and results See Table 4.
PUM
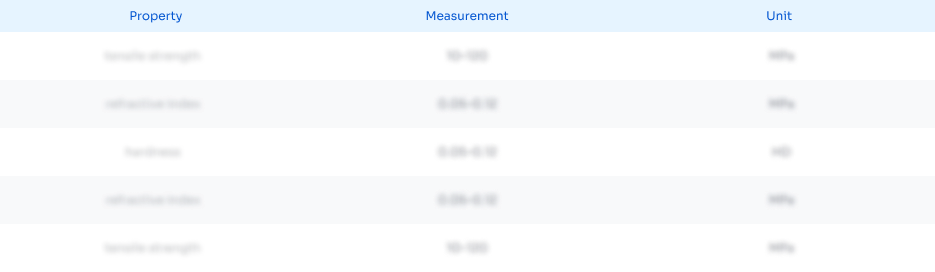
Abstract
Description
Claims
Application Information

- R&D
- Intellectual Property
- Life Sciences
- Materials
- Tech Scout
- Unparalleled Data Quality
- Higher Quality Content
- 60% Fewer Hallucinations
Browse by: Latest US Patents, China's latest patents, Technical Efficacy Thesaurus, Application Domain, Technology Topic, Popular Technical Reports.
© 2025 PatSnap. All rights reserved.Legal|Privacy policy|Modern Slavery Act Transparency Statement|Sitemap|About US| Contact US: help@patsnap.com