Method for supplying refined liquefied gas
A liquefied gas and gas phase technology, applied in refrigeration and liquefaction, container discharge methods, liquefaction, etc., can solve problems such as the increase of non-volatile impurities and the reduction of the remaining amount of liquefied gas
- Summary
- Abstract
- Description
- Claims
- Application Information
AI Technical Summary
Problems solved by technology
Method used
Image
Examples
Embodiment 1
[0315] In Example 1, the use of figure 1 The above-mentioned purification tank (13) of the type shown in the flow chart of the above-mentioned purification of the raw material liquefied ammonia Figure 5 The relationship between the amount of outgassing gas and the reduction in gas phase impurity concentration and liquid phase impurity concentration is shown.
[0316] The concentration of impurity methane contained in the gas phase component in the refining tank (13) was measured by a gas chromatograph GC-PDD (manufactured by GL Science, type: gas chromatograph with a pulse discharge detector), and the concentration of the impurity methane contained in the liquid phase component The concentration of impurity methane in the sample was collected from the liquid phase, the sample was vaporized and homogenized with a vaporizer, and measured with the above-mentioned gas chromatograph.
[0317] (1) Refining device
[0318] The inner volume of the refining tank (13) was 20 liters (...
Embodiment 2
[0338] The liquefied ammonia of the same volatile impurity concentration in the liquefied ammonia was transferred and filled into the refining tank as the raw material liquefied ammonia used in Example 1, and the gas was released from the gas phase part, thereby refining the liquefied ammonia.
[0339] (1) Refining device
[0340] The inner volume of the refining tank (13) was 20 liters (inner diameter 220 mm, height 525 mm).
[0341] The refining apparatus used the same apparatus as that used in Example 1.
[0342] like figure 1 As shown, the storage vessel (11) is connected to the refining tank (13) via the oil removal device (12) through piping in a form that can be filled with liquefied gas, and the discharge passage 3 is connected to the gas phase for measuring the concentration of impurities contained in the gas phase components. A chromatograph (16) is connected, the supply passage 1 is connected to a water removal cartridge (15) filled with an adsorbent capable of re...
Embodiment 3
[0360] The liquefied ammonia of the same volatile impurity concentration in the liquefied ammonia was transferred and filled into the refining tank as the raw material liquefied ammonia used in Example 1, and the gas was released from the gas phase part, thereby refining the liquefied ammonia.
[0361] (1) Refining device
[0362] As a refining device, use figure 2 Siphon type refining tank (34) shown (inner volume: 100 liters, inner diameter: 350 mm, height: 1000 mm).
[0363] In the purification tank ( 34 ), 50 kg of liquefied ammonia, a raw material that is substantially the same as that used in Example 1, was stored in a state maintained at 25° C. and 0.898 MPa.
[0364] The refining tank (34) passes through an oil removal device (35), a pressure reducing valve (36), a vaporizer (37) from a liquid phase extraction valve (32), and a water removal cylinder (38) filled with an adsorbent capable of removing water. )connect. In addition, a CRDS-type moisture meter (17) is c...
PUM
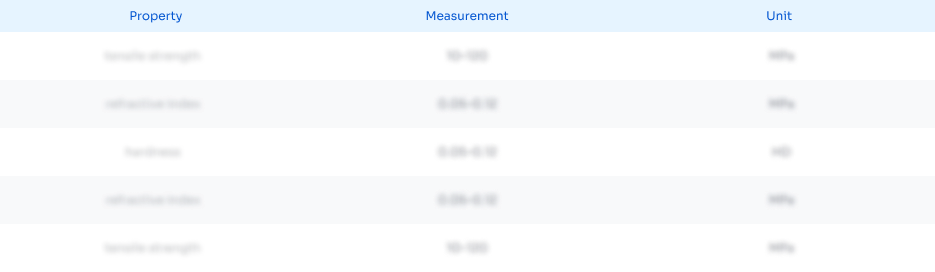
Abstract
Description
Claims
Application Information

- Generate Ideas
- Intellectual Property
- Life Sciences
- Materials
- Tech Scout
- Unparalleled Data Quality
- Higher Quality Content
- 60% Fewer Hallucinations
Browse by: Latest US Patents, China's latest patents, Technical Efficacy Thesaurus, Application Domain, Technology Topic, Popular Technical Reports.
© 2025 PatSnap. All rights reserved.Legal|Privacy policy|Modern Slavery Act Transparency Statement|Sitemap|About US| Contact US: help@patsnap.com