Preparation method of hydrophilic cationic formaldehyde-free fixing agent
An aldehyde-free color-fixing agent, cationic technology, applied in the direction of dyeing, textile and paper making, etc., can solve the problem of the decrease of hydrophilicity of cotton fiber, and achieve the effect of improving hydrophilicity and water absorption.
- Summary
- Abstract
- Description
- Claims
- Application Information
AI Technical Summary
Problems solved by technology
Method used
Examples
Embodiment 1
[0024] 1. Add 30g of the mixture of N,N-diethylallylamine and N,N-dibutylenebutylamine (the weight ratio of the two is 2:1) into the flask, place it in an ice-water bath, and weigh Take 20g of dimethyl sulfate in the dropping funnel, slowly add it dropwise in 30 minutes, control the reaction temperature in the flask to about 60°C, and then stir for 30 minutes;
[0025] Ⅱ. Add 60g of propylene alcohol polyoxyethylene ether, 200g of N-methylethylene ethyl ammonium chloride, 0.04g of ethylenediaminetetraacetic acid disodium salt, and 500g of water in sequence, and stir for 10 minutes;
[0026] Ⅲ. Raise the temperature to 80°C, start to add 8g of ammonium persulfate initiator dropwise, the dropwise addition time is 2h, and keep warm for 2h after the dropwise addition is completed.
[0027] Ⅳ. After the heat preservation is over, adjust the pH value to 6 with liquid caustic soda to obtain a hydrophilic cationic formaldehyde-free color-fixing agent.
Embodiment 2
[0029] 1. Add 60g of the mixture of N,N-diethylallylamine and N,N-dipropylallylbutylamine (the weight ratio of the two substances is 3:1) into the flask, and place it in an ice-water bath. Weigh 70g of benzyl chloride into the dropping funnel, slowly add it dropwise in 60 minutes, control the reaction temperature in the flask to about 40°C, and then stir for 30 minutes;
[0030] Ⅱ. Add 60g of vinyl alcohol polyoxyethylene ether, 600g of N-butylene ethyl ammonium chloride, 0.04g of ethylenediaminetetrapropionic acid sodium salt, 200g of water, and stir for 30min;
[0031] Ⅲ. Raise the temperature to 70°C, start to drop 10g of potassium persulfate initiator, dropwise for 2h, keep warm for 1h after the dropwise addition;
[0032] Ⅳ. After the heat preservation is over, adjust the pH value to 7 with liquid caustic soda to obtain a hydrophilic cationic formaldehyde-free color-fixing agent.
Embodiment 3
[0034] Ⅰ. Add 40g of the mixture of N-methylethyleneethylamine and N-ethyleneethylamine (the weight ratio of the two substances is 1:2) into the flask, place it in an ice-water bath, and weigh 40g of epoxy chlorine Slowly add propane in the dropping funnel for 40 minutes, control the reaction temperature in the flask to about 30°C, and then stir for 40 minutes;
[0035] Ⅱ. Add 180g of diallyl alcohol polyoxyethylene ether, 400g of N-ethylallyl ammonium chloride, 0.1g of aminotriacetic acid sodium salt, and 350g of water in sequence, and stir for 20 minutes;
[0036] Ⅲ. Raise the temperature to 60°C, start to add 20g of azobisisobutylamidine hydrochloride initiator dropwise, the dropwise addition time is 4h, and keep warm for 3h after the dropwise addition is completed.
[0037] Ⅳ. After the heat preservation is over, adjust the pH value to 8 with liquid caustic soda to obtain a hydrophilic cationic formaldehyde-free color-fixing agent.
PUM
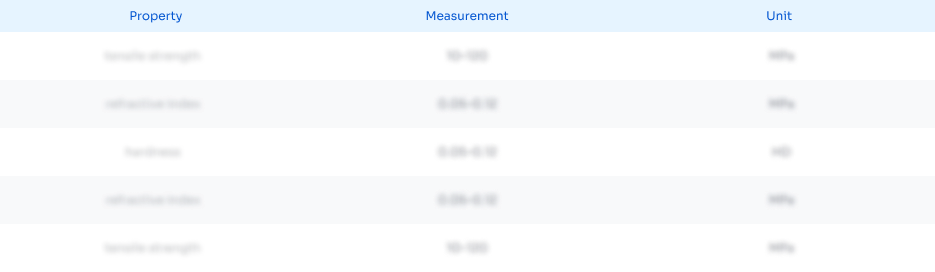
Abstract
Description
Claims
Application Information

- R&D Engineer
- R&D Manager
- IP Professional
- Industry Leading Data Capabilities
- Powerful AI technology
- Patent DNA Extraction
Browse by: Latest US Patents, China's latest patents, Technical Efficacy Thesaurus, Application Domain, Technology Topic, Popular Technical Reports.
© 2024 PatSnap. All rights reserved.Legal|Privacy policy|Modern Slavery Act Transparency Statement|Sitemap|About US| Contact US: help@patsnap.com