High-precision method for controlling uniformity of discharging of extruder
A control method and extruder technology, applied in the field of extruders, can solve problems such as affecting production efficiency, affecting product uniformity and output, affecting product uniformity, etc., so as to improve production efficiency and product quality, and shorten detection and calculation. time, the effect of fine management
- Summary
- Abstract
- Description
- Claims
- Application Information
AI Technical Summary
Problems solved by technology
Method used
Image
Examples
Embodiment Construction
[0024] see figure 1 , the embodiment of a high-precision control method for improving the discharge uniformity of an extruder in the present invention, its implementation system includes an extruder 5, a traction roller 7, a controller 9, a raw material hopper 1, a discharge valve 2 and a scale Measuring device 3, the outlet of raw material hopper 1 is connected with the inlet of weighing device 3 through discharging valve 2, the input end and an output end of controller 9 are respectively connected with the weight signal output end of weighing device 3 and discharging valve 2 Drive connection. The other output end of the controller 9 is connected with the driving motor of the traction roller 7 through the frequency converter 8 (the pulse amount of the servo drive can also be controlled by the controller 9, and the rotation speed of the traction roller 7 can be controlled by the servo motor).
[0025] The screw speed of the extruder 5 is measured by the speed sensor 6 install...
PUM
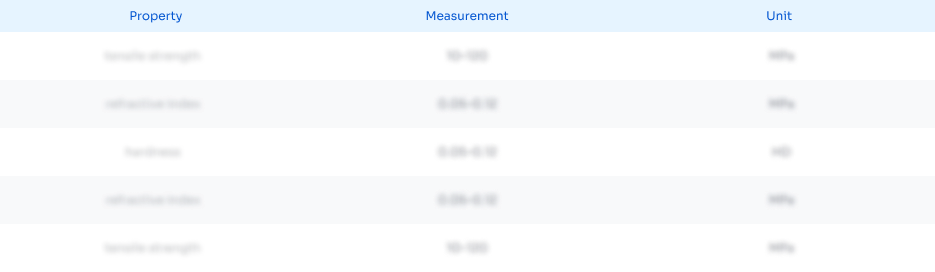
Abstract
Description
Claims
Application Information

- R&D
- Intellectual Property
- Life Sciences
- Materials
- Tech Scout
- Unparalleled Data Quality
- Higher Quality Content
- 60% Fewer Hallucinations
Browse by: Latest US Patents, China's latest patents, Technical Efficacy Thesaurus, Application Domain, Technology Topic, Popular Technical Reports.
© 2025 PatSnap. All rights reserved.Legal|Privacy policy|Modern Slavery Act Transparency Statement|Sitemap|About US| Contact US: help@patsnap.com