Servo control system
A servo control system and programming control technology, applied in the field of servo control systems, can solve problems such as equipment lag, reduced processing efficiency, and complicated wiring, and achieve the effects of reducing failure rates, improving processing efficiency, and saving costs
- Summary
- Abstract
- Description
- Claims
- Application Information
AI Technical Summary
Problems solved by technology
Method used
Image
Examples
Embodiment Construction
[0026] All features disclosed in this specification, or steps in all methods or processes disclosed, may be combined in any manner, except for mutually exclusive features and / or steps.
[0027] Any feature disclosed in this specification (including any appended claims, abstract and drawings), unless expressly stated otherwise, may be replaced by alternative features which are equivalent or serve a similar purpose. That is, unless expressly stated otherwise, each feature is one example only of a series of equivalent or similar features.
[0028] Such as figure 1 with figure 2 As shown, a servo control system of the present invention is used for precision numerical control processing equipment. In the embodiment of the present invention, the present invention is described in detail with a servo control system for a three-dimensional drilling machine tool for steel structures.
[0029] A servo control system includes a programmable control unit with a CANopen communication i...
PUM
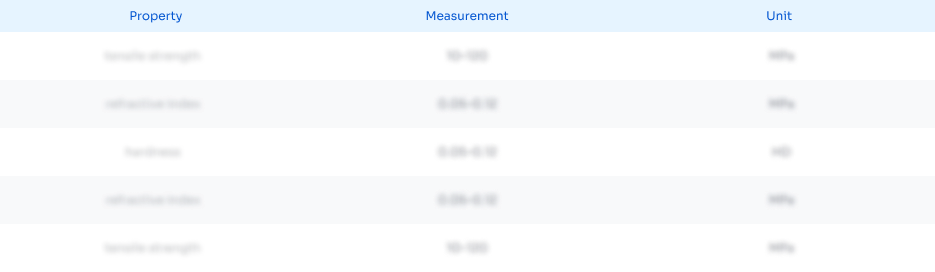
Abstract
Description
Claims
Application Information

- R&D Engineer
- R&D Manager
- IP Professional
- Industry Leading Data Capabilities
- Powerful AI technology
- Patent DNA Extraction
Browse by: Latest US Patents, China's latest patents, Technical Efficacy Thesaurus, Application Domain, Technology Topic, Popular Technical Reports.
© 2024 PatSnap. All rights reserved.Legal|Privacy policy|Modern Slavery Act Transparency Statement|Sitemap|About US| Contact US: help@patsnap.com