High wear resistance steel for knitting needle and manufacture method thereof
A technology with high wear resistance and manufacturing method, which is applied in the field of steel for knitting machinery, can solve the problems of weak fatigue resistance of knitting needles and cannot be well adapted to high-strength operation of knitting, so as to improve microstructure indicators, improve Forgeable shape, the effect of preventing the tendency to crack
- Summary
- Abstract
- Description
- Claims
- Application Information
AI Technical Summary
Problems solved by technology
Method used
Image
Examples
Embodiment 1
[0044] In this example, the composition and weight percentage of cold work die steel are as follows:
[0045] C 1%, Si 0.2%, Mn 0.55%, Cr 0.2%, V 0.1%, Ni 0.1%, Nd 0.1%, P 0.02%, S 0.02%, the balance being Fe and inevitable impurities.
[0046] In this embodiment, the process and steps of cold working die steel are as follows:
[0047] According to the chemical composition ratio of the present invention, a steel ingot cast after melting in an induction furnace is used as a consumable electrode and placed in an electroslag remelting device for electroslag remelting, and the liquid metal falls through the slag layer of the slag pool In the following water-cooled crystallizer, it is re-solidified into steel ingots; the above steel ingots are heated to a temperature range of 1000~1020℃ for 4 hours before forging processing; initial forging temperature: 900~930℃, final forging temperature ≥850℃. After forging, bending, flattening, and milling, the diameter is 0.38mm; the forged steel is ...
PUM
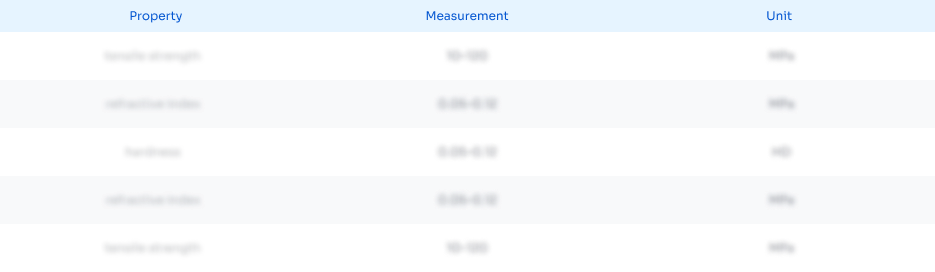
Abstract
Description
Claims
Application Information

- R&D
- Intellectual Property
- Life Sciences
- Materials
- Tech Scout
- Unparalleled Data Quality
- Higher Quality Content
- 60% Fewer Hallucinations
Browse by: Latest US Patents, China's latest patents, Technical Efficacy Thesaurus, Application Domain, Technology Topic, Popular Technical Reports.
© 2025 PatSnap. All rights reserved.Legal|Privacy policy|Modern Slavery Act Transparency Statement|Sitemap|About US| Contact US: help@patsnap.com