Preparation method for mu75 magnetic powder core of ferrosilicon aluminum
A manufacturing method and magnetic powder core technology, applied in the direction of inductance/transformer/magnet manufacturing, magnetic core/yoke, inorganic material magnetism, etc., can solve the problems of unfavorable magnetic powder core, heat treatment temperature limit, removal, etc., to simplify the production process, Increased heat treatment temperature and strong safety effects
- Summary
- Abstract
- Description
- Claims
- Application Information
AI Technical Summary
Problems solved by technology
Method used
Examples
Embodiment 1
[0029] Put industrial pure iron, crystalline silicon, and pure aluminum into a medium-frequency induction furnace with a nominal weight of 150kg for melting at 1600°C, and cast it into an alloy ingot with a chemical composition of 9.10wt% silicon, 5.95wt% aluminum and the balance being iron, and use mechanical crushing method Crushed into pieces below 20mm, the alloy pieces were kept in a hydrogen reduction furnace at 1300°C for 2 hours, then crushed into particles below 5mm with a jaw crusher, and then crushed into powders below 80 mesh by a vibrating ball mill. These powders were placed in a hydrogen reduction furnace at 900°C for 90 minutes for stress relief annealing. According to -100 ~ +200 mesh accounted for 10%, -200 ~ +300 mesh accounted for 70%, -300 mesh accounted for 20% to carry out the powder ratio. Mix the proportioned powder evenly, preheat to 120°C, add an acid solution with 6% alloy powder mass to passivate, the acid solution is an aqueous solution of phospho...
Embodiment 2
[0036] According to the process steps of Example 1, the mass ratio of the binder is adjusted to 0.6%, and the rest of the process conditions remain unchanged. The magnetic properties of the prepared magnetic powder core are as follows:
[0037] ⑴100kHz, 1mT, magnetic permeability μ=72.5;
[0038] ⑵Frequency characteristics:
[0039] f(kHz)
10
100
200
300
500
700
1000
mu
72.53
72.50
72.46
72.44
72.38
72.31
72.29
[0040] (3) When the magnetic permeability drops to 50%, the DC bias field is H=74Oe;
[0041] ⑷Magnetic powder core volume ratio loss: 50kHz, 50mT, P cv =95.3mW / cm3.
Embodiment 3
[0043] According to the process steps of Example 1, the mass ratio of the binder is adjusted to 1.0%, and the rest of the process conditions remain unchanged. The magnetic properties of the prepared magnetic powder core are as follows:
[0044] (1) 100kHz, 1mT, magnetic permeability μ=71.8;
[0045] ⑵Frequency characteristics:
[0046] f(kHz)
10
100
200
300
500
700
1000
mu
72.53
72.50
72.46
72.44
72.38
72.31
72.29
[0047] (3) When the magnetic permeability drops to 50%, the DC bias field is H=76Oe;
[0048] ⑷Magnetic powder core volume ratio loss: 50kHz, 50mT, P cv =96.2mW / cm 3 .
PUM
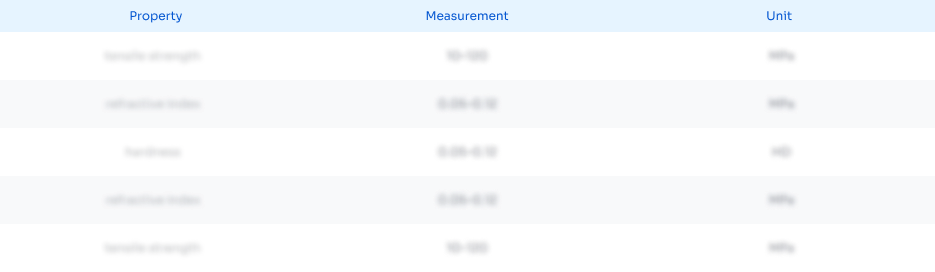
Abstract
Description
Claims
Application Information

- R&D
- Intellectual Property
- Life Sciences
- Materials
- Tech Scout
- Unparalleled Data Quality
- Higher Quality Content
- 60% Fewer Hallucinations
Browse by: Latest US Patents, China's latest patents, Technical Efficacy Thesaurus, Application Domain, Technology Topic, Popular Technical Reports.
© 2025 PatSnap. All rights reserved.Legal|Privacy policy|Modern Slavery Act Transparency Statement|Sitemap|About US| Contact US: help@patsnap.com