Differential pressure type airspeed sensor testing system
A technology of airspeed sensor and test system, which is applied in the test/calibration of speed/acceleration/shock measurement equipment, speed/acceleration/shock measurement, instruments, etc., and can solve the problems of airspeed sensor testing and correction, air velocity and Difficult to control the direction, limited dynamic range of test speed, etc., to achieve the effect of increasing dynamic range and accuracy, low operation and maintenance costs, and low cost
- Summary
- Abstract
- Description
- Claims
- Application Information
AI Technical Summary
Problems solved by technology
Method used
Image
Examples
Embodiment Construction
[0032] In order to make the object, technical solution and advantages of the present invention clearer, the present invention will be described in further detail below in conjunction with specific embodiments and with reference to the accompanying drawings.
[0033] figure 1 It is the overall structure diagram of the differential pressure airspeed sensor testing system of the embodiment of the present invention. Such as figure 1 As shown, the system includes four parts: motion platform subsystem 1, power supply subsystem 2, motor drive subsystem 3, and central controller subsystem 4. Its working principle can be briefly described as: the central controller subsystem 4 sends motion control instructions to the motor drive subsystem 3, and the motor drive subsystem 3 realizes the speed control of the motion platform subsystem 1 according to the instructions, so that the differential pressure air The two sides of the speed sensor 1111 generate a differential pressure, and the di...
PUM
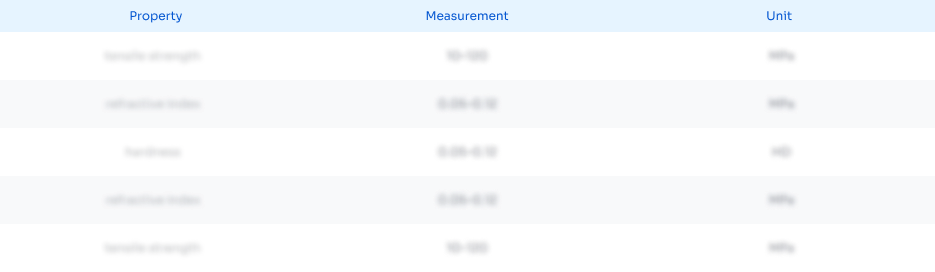
Abstract
Description
Claims
Application Information

- Generate Ideas
- Intellectual Property
- Life Sciences
- Materials
- Tech Scout
- Unparalleled Data Quality
- Higher Quality Content
- 60% Fewer Hallucinations
Browse by: Latest US Patents, China's latest patents, Technical Efficacy Thesaurus, Application Domain, Technology Topic, Popular Technical Reports.
© 2025 PatSnap. All rights reserved.Legal|Privacy policy|Modern Slavery Act Transparency Statement|Sitemap|About US| Contact US: help@patsnap.com