Manufacturing method of resin felt part of automobile engine cover
A technology of automobile engine and manufacturing method, which is applied to vehicle parts, chemical instruments and methods, non-woven fabrics, etc., can solve problems such as potential safety hazards, inconvenient installation, etc. Effect
- Summary
- Abstract
- Description
- Claims
- Application Information
AI Technical Summary
Problems solved by technology
Method used
Examples
Embodiment 1
[0025] A method for manufacturing a resin felt part for an automobile engine cover, the method comprises the manufacture of a semi-finished felt blank and the molding of the part, and the specific steps are as follows:
[0026] a. Manufacturing of semi-finished felt blanks
[0027] (1) Put 50kg cloth flowers and 25kg commercially available ED fiber into the opener to open and mix evenly;
[0028] (2) The uniformly mixed cloth flower and commercially available ED fibers are transported to the air-laid machine, and 25kg of phenolic resin is added thereto to continue mixing, and the mixed material is made into a fiber web through the air-laid machine and is output by a conveyor belt;
[0029] (3) Send the fiber web into the high-temperature drying room with the conveyor belt, control the temperature of the high-temperature drying room at 160° C., and treat at high temperature for 2 minutes to obtain a semi-finished felt blank, which is cut according to size and weighed.
[0030]...
Embodiment 2
[0035] A method for manufacturing a resin felt part for an automobile engine cover, the method comprises the manufacture of a semi-finished felt blank and the molding of the part, and the specific steps are as follows:
[0036] a. Manufacturing of semi-finished felt blanks
[0037] (1) Put 50kg cloth flowers and 30kg commercially available ED fiber into the opener to open and mix evenly;
[0038] (2) The uniformly mixed cloth flowers and commercially available ED fiber are transported to the air-laid machine, and 20kg of phenolic resin is added thereto to continue mixing, and the mixed material is made into a fiber web through the air-laid machine and is output by a conveyor belt;
[0039] (3) Send the fiber web into the high-temperature drying room with the conveyor belt, control the temperature of the high-temperature drying room at 180° C., and treat at high temperature for 1 minute to obtain a semi-finished felt blank, which is cut according to size and weighed.
[0040] ...
Embodiment 3
[0045] A method for manufacturing a resin felt part for an automobile engine cover, the method comprises the manufacture of a semi-finished felt blank and the molding of the part, and the specific steps are as follows:
[0046] a. Manufacturing of semi-finished felt blanks
[0047] (1) Put 70kg cloth flower and 10kg commercially available ED fiber into the opener to open and mix evenly;
[0048] (2) The uniformly mixed cloth flower and commercially available ED fiber are transported to the air-laid machine, and 15kg of phenolic resin is added thereto to continue mixing, and the mixed material is made into a fiber web through the air-laid machine and is output by a conveyor belt;
[0049] (3) Send the fiber web into the high-temperature drying room with the conveyor belt, control the temperature of the high-temperature drying room at 160° C., and treat at high temperature for 2 minutes to obtain a semi-finished felt blank, which is cut according to size and weighed.
[0050] b...
PUM
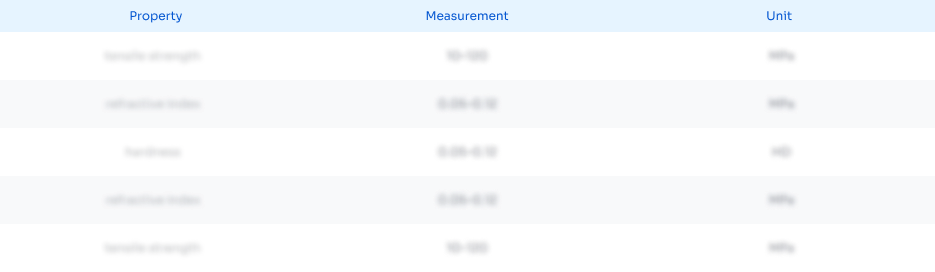
Abstract
Description
Claims
Application Information

- R&D
- Intellectual Property
- Life Sciences
- Materials
- Tech Scout
- Unparalleled Data Quality
- Higher Quality Content
- 60% Fewer Hallucinations
Browse by: Latest US Patents, China's latest patents, Technical Efficacy Thesaurus, Application Domain, Technology Topic, Popular Technical Reports.
© 2025 PatSnap. All rights reserved.Legal|Privacy policy|Modern Slavery Act Transparency Statement|Sitemap|About US| Contact US: help@patsnap.com