Method for producing sulfur hexafluoride by adopting sulfur tetrafluoride oxidation method
A technology of sulfur hexafluoride and sulfur tetrafluoride, which is applied in the fields of chemical instruments and methods, inorganic chemistry, sulfur compounds, etc., and can solve problems such as the inability to obtain sulfur hexafluoride
- Summary
- Abstract
- Description
- Claims
- Application Information
AI Technical Summary
Problems solved by technology
Method used
Image
Examples
Embodiment 1
[0009] Sulfur tetrafluoride is prepared by reacting copper fluoride, silver fluoride or mercury fluoride or their mixture with molten sulfur, and the metal fluoride is converted into sulfide; then oxidize tetrafluoride with oxygen or air at 500-800°C Sulfur is obtained from sulfur hexafluoride, and sulfur dioxide is produced as a by-product; finally, metal sulfide reacts with hydrogen fluoride in the presence of oxygen and then converted into fluoride for recycling, and the by-product sulfur dioxide can be absorbed by sodium hydroxide solution and converted into sodium sulfite for recycling; among them, copper fluoride : silver fluoride: mercury fluoride weight fraction ratio is 1:1-1:1. See the process for details figure 1 .
Embodiment 2
[0011] Sulfur tetrafluoride is prepared by reacting copper fluoride, silver fluoride or mercury fluoride or their mixture with molten sulfur, and the metal fluoride is converted into sulfide; then oxidize tetrafluoride with oxygen or air at 500-800°C Sulfur is obtained from sulfur hexafluoride, and sulfur dioxide is produced as a by-product; finally, metal sulfide reacts with hydrogen fluoride in the presence of oxygen and then converted into fluoride for recycling, and the by-product sulfur dioxide can be absorbed by sodium hydroxide solution and converted into sodium sulfite for recycling; among them, copper fluoride : silver fluoride: mercury fluoride weight fraction ratio is 1:1-2:2. See the process for details figure 1 .
Embodiment 3
[0013] Sulfur tetrafluoride is prepared by reacting copper fluoride, silver fluoride or mercury fluoride or their mixture with molten sulfur, and the metal fluoride is converted into sulfide; then oxidize tetrafluoride with oxygen or air at 500-800°C Sulfur is obtained from sulfur hexafluoride, and sulfur dioxide is produced as a by-product; finally, metal sulfide reacts with hydrogen fluoride in the presence of oxygen and then converted into fluoride for recycling, and the by-product sulfur dioxide can be absorbed by sodium hydroxide solution and converted into sodium sulfite for recycling; among them, copper fluoride : silver fluoride: mercury fluoride weight fraction ratio is 1:2:1. See the process for details figure 1 .
PUM
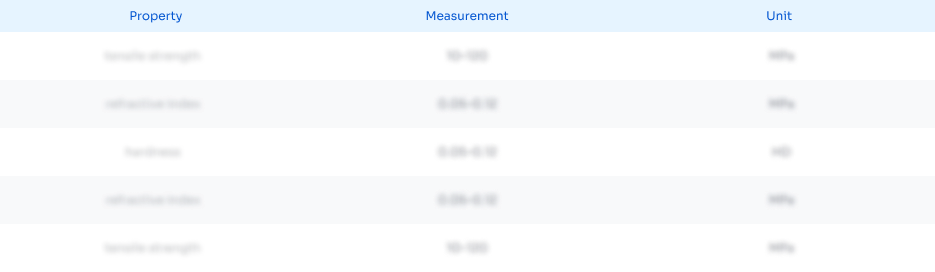
Abstract
Description
Claims
Application Information

- R&D
- Intellectual Property
- Life Sciences
- Materials
- Tech Scout
- Unparalleled Data Quality
- Higher Quality Content
- 60% Fewer Hallucinations
Browse by: Latest US Patents, China's latest patents, Technical Efficacy Thesaurus, Application Domain, Technology Topic, Popular Technical Reports.
© 2025 PatSnap. All rights reserved.Legal|Privacy policy|Modern Slavery Act Transparency Statement|Sitemap|About US| Contact US: help@patsnap.com