Residual oil hydrogenation treatment and catalytic cracking combined method
A catalytic cracking and hydrotreating technology, applied in hydrotreating process, hydrocarbon oil treatment, petroleum industry, etc., can solve problems such as limited yield of naphtha and diesel, low cracking rate of residual oil, increased investment cost, etc., to achieve Eliminate repeated processing steps, reduce equipment investment, and improve utilization
- Summary
- Abstract
- Description
- Claims
- Application Information
AI Technical Summary
Problems solved by technology
Method used
Image
Examples
Embodiment
[0031] This embodiment adopts the combination method of residual oil hydrotreating and catalytic cracking provided by the present invention, and the liquid phase product obtained by hydrotreating is fractionally distilled into hydrogenated naphtha, diesel oil and hydrogenated tail oil, hydrogenated naphtha and hydrogenated tail oil. The oil enters the catalytic cracking unit together, and the catalytic cracking reaction effluent fractionation system simplifies the design, only the dry gas, liquefied gas and gasoline fractions are fractionated, and the catalytic cracking diesel oil, catalytic cycle oil and catalytic oil slurry are directly used as catalytic cracking heavy fractions without fractionation. The heavy distillates from catalytic cracking are recycled to the hydrotreating unit for further processing after filtering out solid impurities. Table 2, Table 3, and Table 5 are process conditions, product distribution, and main product properties, respectively.
[0032] Cont...
PUM
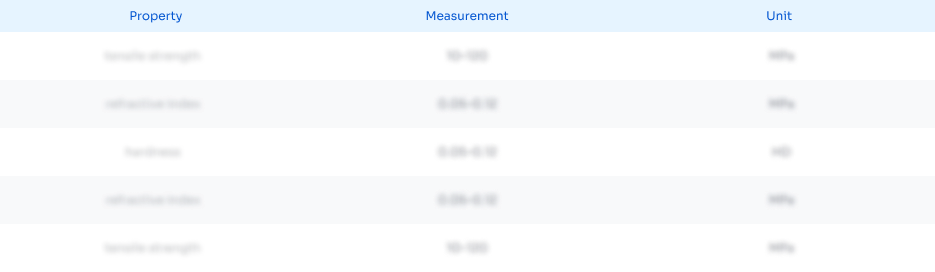
Abstract
Description
Claims
Application Information

- R&D
- Intellectual Property
- Life Sciences
- Materials
- Tech Scout
- Unparalleled Data Quality
- Higher Quality Content
- 60% Fewer Hallucinations
Browse by: Latest US Patents, China's latest patents, Technical Efficacy Thesaurus, Application Domain, Technology Topic, Popular Technical Reports.
© 2025 PatSnap. All rights reserved.Legal|Privacy policy|Modern Slavery Act Transparency Statement|Sitemap|About US| Contact US: help@patsnap.com