A kind of method of producing pyridine compound
A technology of compound and pyridine, which is applied in the field of liquid-phase continuous preparation of pyridine compounds mainly composed of 3-picoline, can solve the problems of easy deactivation of catalysts, and achieve the effects of improving production efficiency, improving utilization rate and saving energy
- Summary
- Abstract
- Description
- Claims
- Application Information
AI Technical Summary
Problems solved by technology
Method used
Image
Examples
Embodiment 1
[0022] Four 2L autoclaves are used to form a reactor according to the process flow chart. Add 500 grams of catalyst to the first three autoclaves, respectively add 1200 grams of 50% ethanol aqueous solution to the four autoclaves, start stirring, and heat up to 228 ° C. Turn on the high-pressure metering pumps of No. 1, No. 2, and No. 3 autoclaves, and inject the pre-prepared raw materials (aqueous solution containing 16.3% urotropine, 32% paraldehyde, and 31% ethanol) into the first three autoclaves respectively. Inside, the control pressure is 4.0Mpa. The flow rates are 400 g / h, 350 g / h, and 300 g / h respectively, and the No. 4 autoclave keeps the liquid level stable. Continuous feed 300 hours, obtain altogether 48.99 kilograms of 3-methylpyridines, 1.06 kilograms of pyridines, 2.25 kilograms of 2,5-lutidines, 2.52 kilograms of 3,5-lutidines, 6.63 kilograms of 3-ethylpyridines, 0.8 kg of 2-methyl-5-ethylpyridine.
Embodiment 2
[0024] Four 2L autoclaves are used to form a reactor according to the process flow chart. Add 500 grams of catalyst to the first three autoclaves, respectively add 1200 grams of 50% ethanol aqueous solution to the four autoclaves, start stirring, and heat up to 232 ° C. Turn on the high-pressure metering pumps of No. 1, No. 2, and No. 3 autoclaves, and inject the pre-prepared raw materials (aqueous solution containing 16.3% urotropine, 32% paraldehyde, and 31% ethanol) into the first three autoclaves respectively. Inside. The flow rate is 500 g / h, 450 g / h, 400 g / h respectively, the control pressure is 4.3Mpa, and the No. 4 autoclave keeps the liquid level stable. Continuous feed 300 hours, obtain altogether 54.54 kilograms of 3-methylpyridines, 1.18 kilograms of pyridines, 2.51 kilograms of 2,5-lutidines, 2.83 kilograms of 3,5-lutidines, 7.38 kilograms of 3-ethylpyridines, 0.89 kg of 2-methyl-5-ethylpyridine.
Embodiment 3
[0026] Four 2L autoclaves are used to form a reactor according to the process flow chart. Add 500 grams of catalyst to the first three autoclaves, respectively add 1200 grams of 50% ethanol aqueous solution to the four autoclaves, start stirring, and heat up to 220 ° C. Turn on the high-pressure metering pumps of No. 1, No. 2, and No. 3 autoclaves, and inject the pre-prepared raw materials (aqueous solution containing 16.3% urotropine, 32% paraldehyde, and 31% ethanol) into the first three autoclaves respectively. Inside. The flow rate is 400 g / h, 350 g / h, 300 g / h respectively, the control pressure is 3.6Mpa, and the No. 4 autoclave keeps the liquid level stable. Continuous feed 300 hours, obtain altogether 41.39 kilograms of 3-methylpyridines, 0.95 kilograms of pyridines, 1.98 kilograms of 2,5-lutidines, 2.12 kilograms of 3,5-lutidines, 6.01 kilograms of 3-ethylpyridines, 0.71 kg of 2-methyl-5-ethylpyridine.
PUM
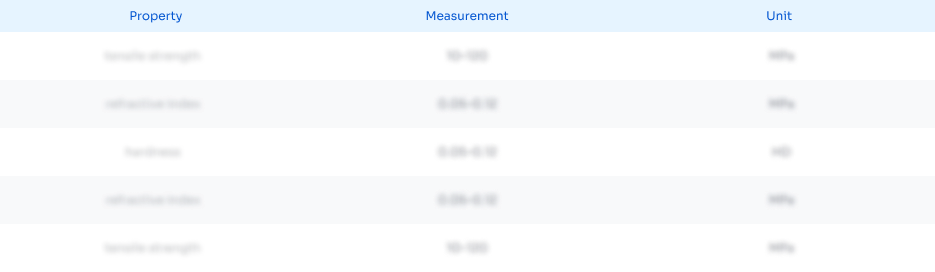
Abstract
Description
Claims
Application Information

- R&D
- Intellectual Property
- Life Sciences
- Materials
- Tech Scout
- Unparalleled Data Quality
- Higher Quality Content
- 60% Fewer Hallucinations
Browse by: Latest US Patents, China's latest patents, Technical Efficacy Thesaurus, Application Domain, Technology Topic, Popular Technical Reports.
© 2025 PatSnap. All rights reserved.Legal|Privacy policy|Modern Slavery Act Transparency Statement|Sitemap|About US| Contact US: help@patsnap.com