A method for removing carbon impurities by silicon carbide micropowder
A technology of silicon carbide micropowder and carbon impurities, which is applied in the field of purification of silicon-containing compounds, can solve the problems of introducing carbon impurities, etc., achieve the effects of simple process, low equipment dependence, and improved cutting quality
- Summary
- Abstract
- Description
- Claims
- Application Information
AI Technical Summary
Problems solved by technology
Method used
Examples
Embodiment 1
[0024] The invention is a method for removing carbon impurities by silicon carbide micropowder. The method for removing carbon impurities comprises the following steps:
[0025] The first step: inject 1200# silicon carbide micropowder into water to make slurry, add 400kg of micropowder into 1m 3 Water, the slurry mass percentage concentration is 28.5wt%, add 300g of dispersant sodium carboxymethylcellulose, add acetic acid to adjust the pH value to 6, and fully stir with a forced mixer;
[0026] The second step: use a horizontal screw centrifuge, the centrifugal speed is 800r / min, and the centrifugal time is 3min, so that the moisture content is reduced to below 20%;
[0027] Step 3: re-inject the slurry obtained in the previous step to make slurry, and add 400kg of primary slurry to 1.2m 3 Water, slurry mass percentage concentration is 25wt%
[0028] Step 4: inject the above slurry into the hydraulic classification device, add 160ml of tertiary alcohol oil for flotation, an...
Embodiment 2
[0032] The invention is a method for removing carbon impurities by silicon carbide micropowder. The method for removing carbon impurities comprises the following steps:
[0033] Step 1: Inject 1200# silicon carbide micropowder into water to make slurry, add 400kg of micropowder to 2m 3 Water, the slurry mass percentage concentration is 16.67wt%, add 480g of dispersant sodium hexametapolyphosphate, add oxalic acid to adjust the pH value to 6.5, and fully stir with a forced mixer;
[0034] The second step: using a sedimentation centrifuge, the centrifugal speed is 800r / min, and the centrifugal time is 3min, so that the moisture content is reduced to below 20%;
[0035] The third step: re-inject the slurry obtained in the previous step to make slurry, and add 400kg of primary slurry to 0.6m 3 Water, the slurry mass percentage concentration is 40wt%;
[0036] Step 4: Inject the above slurry into the hydraulic classification device, add 100ml of flotation oil oleic acid, and cont...
Embodiment 3
[0040] The invention is a method for removing carbon impurities by silicon carbide micropowder. The method for removing carbon impurities comprises the following steps:
[0041] Step 1: Inject 1500# silicon carbide micropowder into water to make slurry, add 400kg of micropowder to 2m 3 Water, the mass percentage concentration of the slurry is 16.67wt%, add 250g of dispersant gum arabic, add acetic acid to adjust the pH value to 6.5, and fully stir with a forced mixer;
[0042] The second step: using a horizontal centrifuge, the centrifugal speed is 800r / min, and the centrifugal time is 3min, so that the moisture content is reduced to below 20%;
[0043] Step 3: re-inject the slurry obtained in the previous step to make slurry, and add 400kg of primary slurry to 1.2m 3 Water, the slurry mass percentage concentration is 25wt%;
[0044] Step 4: inject the above slurry into the hydraulic classification device, add 240ml of terpineol oil for flotation, and continuously blow in 23...
PUM
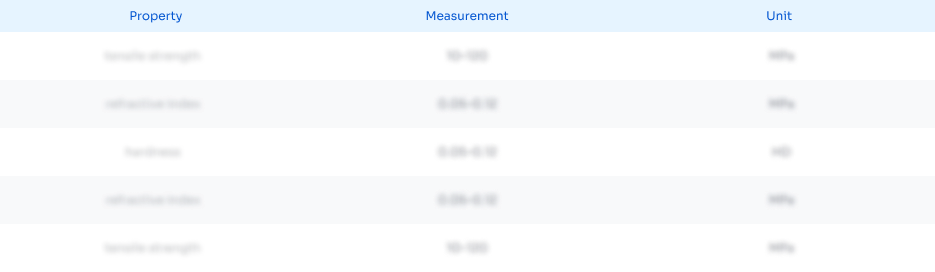
Abstract
Description
Claims
Application Information

- Generate Ideas
- Intellectual Property
- Life Sciences
- Materials
- Tech Scout
- Unparalleled Data Quality
- Higher Quality Content
- 60% Fewer Hallucinations
Browse by: Latest US Patents, China's latest patents, Technical Efficacy Thesaurus, Application Domain, Technology Topic, Popular Technical Reports.
© 2025 PatSnap. All rights reserved.Legal|Privacy policy|Modern Slavery Act Transparency Statement|Sitemap|About US| Contact US: help@patsnap.com