A kind of honeycomb sound-absorbing panel and its production process
A sound-absorbing panel and honeycomb technology, applied in the field of building materials, can solve problems such as easy deformation, high construction cost, affecting project quality and aesthetics, and achieve the effect of light weight and high noise reduction coefficient
- Summary
- Abstract
- Description
- Claims
- Application Information
AI Technical Summary
Problems solved by technology
Method used
Image
Examples
Embodiment 1
[0023] Such as figure 1 and figure 2 As shown, a honeycomb sound-absorbing panel of the present invention includes a three-layer structure, the middle layer is a hexagonal honeycomb core 1, and a support sheet 2 is arranged on the top of the hexagonal honeycomb core 1; microporous aluminum plates are evenly distributed under the hexagonal honeycomb core 1 3. Its supporting sheet 2 is an aluminum plate. The upper and lower surfaces of the hexagonal honeycomb core 1 are all sealed by non-woven fabric 4 . Its hexagonal honeycomb core 1 is composed of several closed hexagonal honeycomb cavities 11 . Its hexagonal honeycomb core 1 adopts PVC to make. Its hexagonal honeycomb cavity 11 is filled with sound-absorbing material 5 . Its described sound-absorbing material 5 is rock wool. The upper and lower surfaces of the hexagonal honeycomb core 1 are combined with the non-woven fabric 4 by gluing.
[0024] Production Process:
[0025] (1) Material preparation: hexagonal honeyc...
Embodiment 2
[0031] Such as figure 1 and figure 2 As shown, a honeycomb sound-absorbing panel of the present invention includes a three-layer structure, the middle layer is a hexagonal honeycomb core 1, and a support sheet 2 is arranged on the top of the hexagonal honeycomb core 1; microporous aluminum plates are evenly distributed under the hexagonal honeycomb core 1 3. Its supporting thin plate 2 is a plastic plate. The upper and lower surfaces of the hexagonal honeycomb core 1 are all sealed by non-woven fabric 4 . Its hexagonal honeycomb core 1 is composed of several closed hexagonal honeycomb cavities 11 . Its hexagonal honeycomb core 1 adopts PVC to make. Its hexagonal honeycomb cavity 11 is filled with sound-absorbing material 5 . Its described sound-absorbing material 5 is perlite. The upper and lower surfaces of the hexagonal honeycomb core 1 are combined with the non-woven fabric 4 by gluing.
Embodiment 3
[0033] Such as figure 1 and figure 2 As shown, a honeycomb sound-absorbing panel of the present invention includes a three-layer structure, the middle layer is a hexagonal honeycomb core 1, and a support sheet 2 is arranged on the top of the hexagonal honeycomb core 1; microporous aluminum plates are evenly distributed under the hexagonal honeycomb core 1 3. Its supporting sheet 2 is a PVC foam board. The upper and lower surfaces of the hexagonal honeycomb core 1 are all sealed by non-woven fabric 4 . Its hexagonal honeycomb core 1 is composed of several closed hexagonal honeycomb cavities 11 . Its hexagonal honeycomb core 1 adopts PVC to make. Its hexagonal honeycomb cavity 11 is filled with sound-absorbing material 5 . Its described sound-absorbing material 5 is rock wool. The upper and lower surfaces of the hexagonal honeycomb core 1 are combined with the non-woven fabric 4 by gluing.
PUM
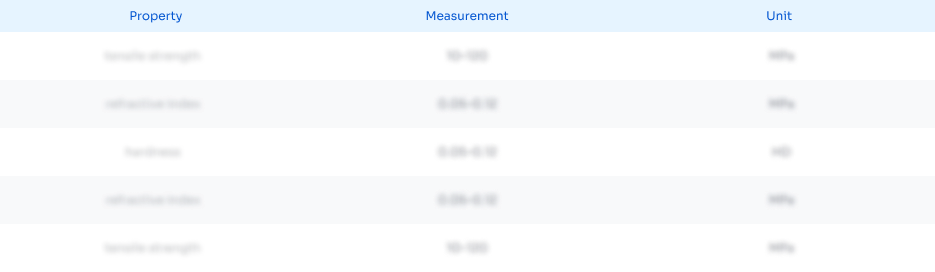
Abstract
Description
Claims
Application Information

- R&D Engineer
- R&D Manager
- IP Professional
- Industry Leading Data Capabilities
- Powerful AI technology
- Patent DNA Extraction
Browse by: Latest US Patents, China's latest patents, Technical Efficacy Thesaurus, Application Domain, Technology Topic, Popular Technical Reports.
© 2024 PatSnap. All rights reserved.Legal|Privacy policy|Modern Slavery Act Transparency Statement|Sitemap|About US| Contact US: help@patsnap.com