Laser electronic target based on non-diffraction light
A non-diffraction, laser technology, used in instruments, mapping and navigation, measuring devices, etc., can solve the problems of the reduction of target system accuracy and working stability, the limitation of the system's spatial angle measurement accuracy, and the influence of laser spot center coordinates, etc. Achieve the effect of reducing development intensity, strong anti-environmental light interference ability, and easy engineering implementation
- Summary
- Abstract
- Description
- Claims
- Application Information
AI Technical Summary
Problems solved by technology
Method used
Image
Examples
Embodiment Construction
[0018] The preferred embodiments of the present invention will be further described in detail below in conjunction with the accompanying drawings.
[0019] Such as figure 1 As shown, the specific devices needed to realize this example: a beam splitter 4 with a transmittance of 50%, two plane mirrors 3 and 5, a damped gravity pendulum 6, a conical lens 2 and a cube-corner pyramid lens 7, cubic The upper and lower bottom surfaces of the pyramidal prism lens are parallel, and a CCD image sensor is used to capture the non-diffraction light spot.
[0020] The photosensitive surface of the CCD image sensor 1 and the bottom plane of the conical lens 2 are parallel to each other and the center is coaxial, and form an angle of 45 degrees with the beam splitter 4. The plane mirror surface 5 is fixed on the damped gravity pendulum 6, under the action of the damped gravity pendulum, its plane normal does not change with the rolling of the target, and always remains in the direction of gravity....
PUM
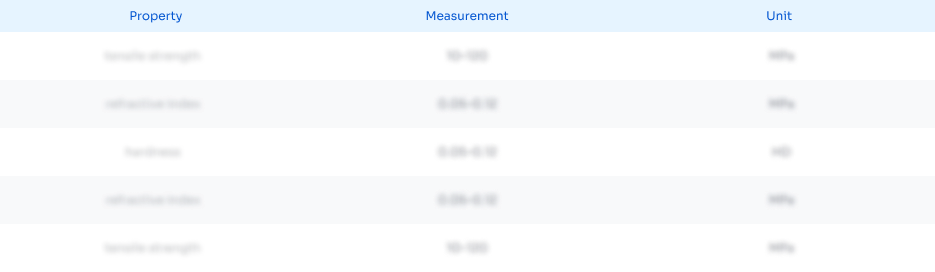
Abstract
Description
Claims
Application Information

- R&D
- Intellectual Property
- Life Sciences
- Materials
- Tech Scout
- Unparalleled Data Quality
- Higher Quality Content
- 60% Fewer Hallucinations
Browse by: Latest US Patents, China's latest patents, Technical Efficacy Thesaurus, Application Domain, Technology Topic, Popular Technical Reports.
© 2025 PatSnap. All rights reserved.Legal|Privacy policy|Modern Slavery Act Transparency Statement|Sitemap|About US| Contact US: help@patsnap.com