Chain Tensioner
A technology for tensioners and chains, applied in belts/chains/gears, mechanical equipment, transmissions, etc., which can solve the shape that is difficult to assemble and disassemble, the rattling effect is small, and the shape of the tensioner body is large, etc. problem, achieve miniaturization and reduce manufacturing cost
- Summary
- Abstract
- Description
- Claims
- Application Information
AI Technical Summary
Problems solved by technology
Method used
Image
Examples
no. 1 Embodiment
[0104] Hereinafter, the chain tensioner according to the first embodiment of the present invention will be described based on the drawings.
[0105] in, figure 1 It is a usage diagram of the chain tensioner according to the first embodiment of the present invention, figure 2 It is a schematic cross-sectional view showing the chain tensioner according to the first embodiment of the present invention, image 3 It is a front view of the chain tensioner according to the first embodiment of the present invention, Figure 4 for figure 2 Schematic diagram of the plunger used in the chain tensioner shown, Figure 5 is the schematic diagram and partial enlarged diagram of the elastic ring, Figure 6 for figure 2 An enlarged illustration of the ratchet mechanism of the chain tensioner shown, Figure 7 for Figure 5 Illustration of the ring deformation characteristics of the shown elastic ring. in addition, Figure 8 to Figure 9 It is an operation diagram when a load in the ...
no. 2 Embodiment
[0143] Hereinafter, a chain tensioner 200 according to a second embodiment of the present invention will be described based on the drawings.
[0144] Figure 22 It is a schematic cross-sectional view showing the chain tensioner according to the second embodiment of the present invention, Figure 23 It is a front view of the chain tensioner according to the second embodiment of the present invention.
[0145] Fig. 24 is the elastic ring used in the second embodiment of the present invention, (a) is its front view, (b) is its side view.
[0146] Here, comparing the chain tensioner 200 of the second embodiment of the present invention with the chain tensioner 100 of the first embodiment above, only the specific form of the elastic ring 230 is different, and the other device structures are the same as those of the first embodiment. The chain tensioner 100 described in the embodiment is completely the same, therefore, for these specific descriptions, it is sufficient to replace t...
no. 3 Embodiment
[0153] Hereinafter, a chain tensioner 300 according to a third embodiment of the present invention will be described based on the drawings.
[0154] Figure 25 It is a usage diagram and an enlarged view of main parts of the chain tensioner according to the third embodiment of the present invention.
[0155] Here, comparing the chain tensioner 300 according to the third embodiment of the present invention with the chain tensioner 100 according to the above-mentioned first embodiment, only the specific forms of the tensioner body 310 and the one-way valve mechanism 350 are different. The other device structures are the same as those of the chain tensioner 100 described in the first embodiment. Therefore, for these specific descriptions, it is sufficient to replace the reference numeral 100 with 300 , and the same descriptions will be omitted here.
[0156] in addition, Figure 25 The symbol E shown is the engine block wall at the position where the chain tensioner 300 accordin...
PUM
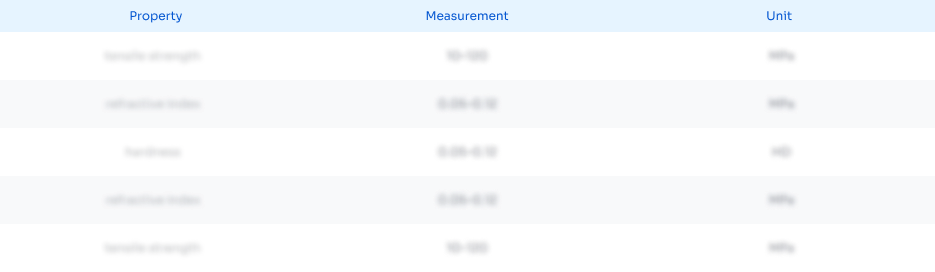
Abstract
Description
Claims
Application Information

- R&D
- Intellectual Property
- Life Sciences
- Materials
- Tech Scout
- Unparalleled Data Quality
- Higher Quality Content
- 60% Fewer Hallucinations
Browse by: Latest US Patents, China's latest patents, Technical Efficacy Thesaurus, Application Domain, Technology Topic, Popular Technical Reports.
© 2025 PatSnap. All rights reserved.Legal|Privacy policy|Modern Slavery Act Transparency Statement|Sitemap|About US| Contact US: help@patsnap.com