Chlorinated natural rubber paint added with modified graphite and preparation method thereof
A technology of chlorinated natural rubber and chlorinated rubber, which is applied in the direction of rubber derivative coatings and coatings, and can solve the problems of poor thermal stability of chlorinated rubber
- Summary
- Abstract
- Description
- Claims
- Application Information
AI Technical Summary
Problems solved by technology
Method used
Examples
Embodiment 1
[0008] Take 200g of the prepared graphite oxide and disperse it in 4L of ethanol. After stirring evenly, add 100g of nonylamine, under mechanical stirring, react at 20 degrees for 12 hours, and then centrifuge. The resulting precipitate is washed repeatedly with ethanol, centrifuged again, and collected Obtain modified graphite.
[0009] Take pre-modified graphite (100g to 200g) and add it to 500ml xylene, and stir evenly. Another 2 kg of chlorinated rubber powder was dissolved in 10 L of toluene, xylene and butyl acetate mixed solvent. Finally, mix the dispersion of modified graphite, chlorinated rubber solution, 50% phenolic resin solution (1L to 1.5L) and chlorinated paraffin-42 (0.1 to 0.15kg), high shear dispersion (10000r / min) for 10min, Filter to get the finished paint. The performance tests of all coatings are tested in accordance with national standards. The test results show that the coating adhesion is grade 3, the impact strength is 50cm, the pencil hardness is ...
Embodiment 2
[0011] Take 200g of the prepared graphite oxide and disperse it in 4L of methanol, stir evenly, add 100g of laurylamine, under mechanical stirring, react at 20 degrees for 12 hours, then centrifuge, the obtained precipitate is washed repeatedly with ethanol, centrifuged again, and collected Obtain modified graphite.
[0012] Take pre-modified graphite (100g to 200g) and add it to 500ml xylene, and stir evenly. Another 2 kg of chlorinated rubber powder was dissolved in 10 L of toluene, xylene and butyl acetate mixed solvent. Finally, mix the dispersion of modified graphite, chlorinated rubber solution, 50% phenolic resin solution (1L to 1.5L) and chlorinated paraffin-42 (0.1 to 0.15kg), high shear dispersion (10000r / min) for 10min, Filter to get the finished paint. The performance tests of all coatings are tested in accordance with national standards. The test results show that the coating adhesion is grade 3, the impact strength is 50cm, the pencil hardness is 2H, and the c...
Embodiment 3
[0014] Get 200g of the prepared graphite oxide and disperse it in 4L of acetone, after stirring evenly, add 100g of p-n-butylaniline, under mechanical stirring, react at 20 degrees for 12 hours, then centrifuge, and the obtained precipitate is washed repeatedly with ethanol, and then Centrifuge to collect modified graphite.
[0015] Take pre-modified graphite (100g to 200g) and add it to 500ml xylene, and stir evenly. Another 2 kg of chlorinated rubber powder was dissolved in 10 L of toluene, xylene and butyl acetate mixed solvent. Finally, mix the dispersion of modified graphite, chlorinated rubber solution, 50% phenolic resin solution (1L to 1.5L) and chlorinated paraffin-42 (0.1 to 0.15kg), high shear dispersion (10000r / min) for 10min, Filter to get the finished paint. The performance tests of all coatings are tested in accordance with national standards. The test results show that the coating adhesion is grade 3, the impact strength is 50cm, the pencil hardness is 3H, a...
PUM
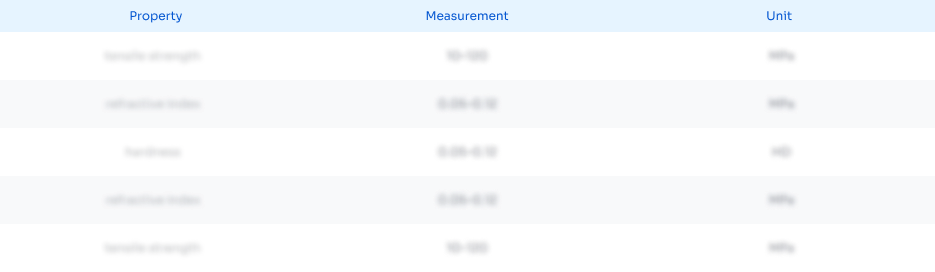
Abstract
Description
Claims
Application Information

- R&D
- Intellectual Property
- Life Sciences
- Materials
- Tech Scout
- Unparalleled Data Quality
- Higher Quality Content
- 60% Fewer Hallucinations
Browse by: Latest US Patents, China's latest patents, Technical Efficacy Thesaurus, Application Domain, Technology Topic, Popular Technical Reports.
© 2025 PatSnap. All rights reserved.Legal|Privacy policy|Modern Slavery Act Transparency Statement|Sitemap|About US| Contact US: help@patsnap.com