MDOF (multiple-degree-of-freedom) magnetic suspension motor
A magnetic levitation and degree of freedom technology, applied in the direction of electrical components, magnetic attraction or thrust holding devices, etc., can solve the problems that the transmission mechanism affects the positioning accuracy of the manipulator, destroys the stability of the system, and the manipulator is large in size, and achieves light weight, The effect of simple structure and small volume
- Summary
- Abstract
- Description
- Claims
- Application Information
AI Technical Summary
Problems solved by technology
Method used
Image
Examples
specific Embodiment approach 1
[0041] Specific implementation mode one, see figure 1 , 2 This embodiment will be described. The multi-degree-of-freedom magnetic levitation motor described in this embodiment is a spherical motor, which includes a rotating motor unit and a deflection and levitation motor unit,
[0042] The rotating electrical machine unit is composed of a stator and a rotor, the stator includes an armature core 15 and a multi-phase armature winding, the rotor includes a rotor yoke 23 and a rotor permanent magnet 24, and the rotating electrical machine unit is an outer rotor structure;
[0043] The deflection and levitation motor unit includes a primary and a secondary, the primary comprises a deflection control winding, a levitation control winding and a primary iron core 13, the secondary yoke 21 includes a secondary yoke 21 and a secondary permanent magnet 22, and the deflection and levitation motor unit is the outer substructure,
[0044] The armature iron core 15 of the rotary motor un...
specific Embodiment approach 2
[0049] Embodiment 2. This embodiment is a further limitation of the multi-degree-of-freedom magnetic levitation motor described in Embodiment 1. In this embodiment, the effective side of each rotating armature coil 14 is embedded in the armature core 15 . Embedding the rotating armature coil 14 in the iron core can increase the magnetic field intensity generated by the coil, that is, when the same current flows through the coil, the magnetic field intensity generated by the coil will be greater after being embedded in the iron core.
specific Embodiment approach 3
[0050] Embodiment 3. This embodiment is a further limitation of the multi-degree-of-freedom magnetic levitation motor described in Embodiment 1. In this embodiment, each rotating armature coil 14 is embedded in an armature core 15 .
PUM
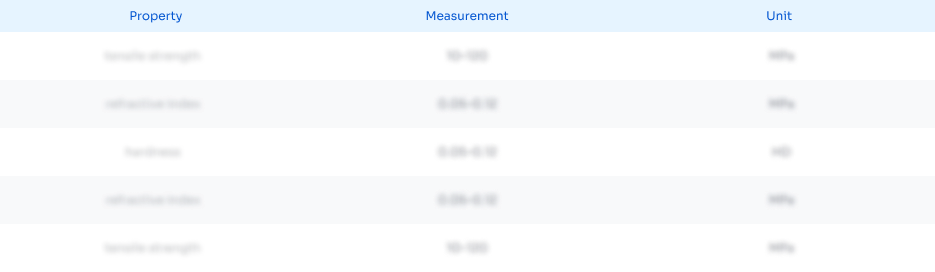
Abstract
Description
Claims
Application Information

- R&D
- Intellectual Property
- Life Sciences
- Materials
- Tech Scout
- Unparalleled Data Quality
- Higher Quality Content
- 60% Fewer Hallucinations
Browse by: Latest US Patents, China's latest patents, Technical Efficacy Thesaurus, Application Domain, Technology Topic, Popular Technical Reports.
© 2025 PatSnap. All rights reserved.Legal|Privacy policy|Modern Slavery Act Transparency Statement|Sitemap|About US| Contact US: help@patsnap.com