Starch composite foamed material and its production method
A technology of composite foaming and composite foaming agent, which is applied in the field of starch composite foaming material and its preparation, can solve the problems such as difficulty in molding and processing of starch, and achieve the effects of simple process, strong operability and environmental protection.
- Summary
- Abstract
- Description
- Claims
- Application Information
AI Technical Summary
Problems solved by technology
Method used
Image
Examples
Embodiment 1~3
[0028] Take each raw material according to the raw material composition in Table 1, first add starch and plasticizer to a high-speed mixer and stir for 20 minutes at room temperature to obtain plasticized starch, and then add the plasticized starch and all other raw materials to the internal mixer, Mix at 100°C for 15 minutes to obtain pre-plasticized materials, then enter the open mixer, knead evenly at 80°C, and completely plasticize to obtain plasticized materials, and finally add extruder to granulate at 120°C to obtain The pellets are air-cooled to obtain the starch composite foaming material.
[0029]
[0030] Among them, the elastomer is POE, the inorganic powder is talcum powder and kaolin, the ratio of talc powder and kaolin is 10:1, the plasticizer is glycerin and absolute ethanol, and the ratio of glycerin and absolute ethanol is 2:1. The agent is dicumyl peroxide, the blowing agent is azodicarbonamide and sodium bicarbonate, the ratio of azodicarbonamide and sod...
Embodiment 4~6
[0032] According to the composition of the raw materials in Table 2, each raw material was taken, and the processing steps and process parameters were the same as in Example 1 to obtain a starch composite foaming material.
[0033]
[0034] Among them, the elastomer is POE, the inorganic powder is talcum powder and kaolin, the ratio of talc powder and kaolin is 10:1, the plasticizer is glycerin and absolute ethanol, and the ratio of glycerin and absolute ethanol is 2:1, cross-linking The agent is dicumyl peroxide, the blowing agent is azodicarbonamide and sodium bicarbonate, the ratio of azodicarbonamide and sodium bicarbonate is 3.5:1.5, the surface treatment agent is silane coupling agent, solubilizer For epoxy resins and vinyl acrylates. The ratio of epoxy resin to ethylene acrylate is 1:2, other additives are zinc oxide and zinc stearate, and the ratio of zinc oxide to zinc stearate is 2.5:1.
Embodiment 7~9
[0036] According to the composition of the raw materials in Table 3, each raw material was taken, and the processing steps and process parameters were the same as in Example 1 to obtain a starch composite foaming material.
[0037]
[0038] Among them, the elastomer is POE, the inorganic powder is talcum powder and kaolin, the ratio of talc powder and kaolin is 10:1, the plasticizer is glycerin and absolute ethanol, and the ratio of glycerin and absolute ethanol is 2:1, cross-linking The agent is dicumyl peroxide, the blowing agent is azodicarbonamide and sodium bicarbonate, the ratio of azodicarbonamide and sodium bicarbonate is 3.5:1.5, the surface treatment agent is silane coupling agent, solubilizer For epoxy resins and vinyl acrylates. The ratio of epoxy resin to ethylene acrylate is 1:2, other additives are zinc oxide and zinc stearate, and the ratio of zinc oxide to zinc stearate is 2.5:1.
PUM
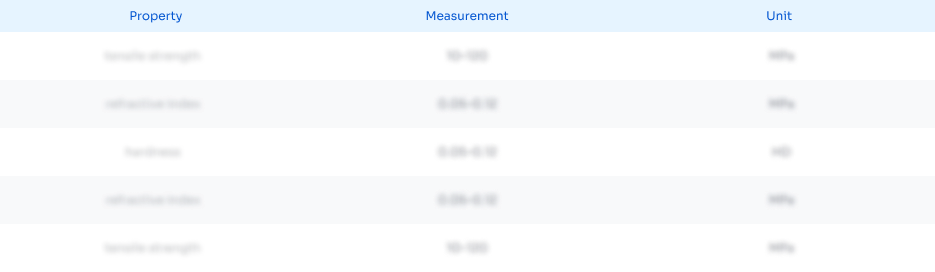
Abstract
Description
Claims
Application Information

- Generate Ideas
- Intellectual Property
- Life Sciences
- Materials
- Tech Scout
- Unparalleled Data Quality
- Higher Quality Content
- 60% Fewer Hallucinations
Browse by: Latest US Patents, China's latest patents, Technical Efficacy Thesaurus, Application Domain, Technology Topic, Popular Technical Reports.
© 2025 PatSnap. All rights reserved.Legal|Privacy policy|Modern Slavery Act Transparency Statement|Sitemap|About US| Contact US: help@patsnap.com