Calculation verification method for torsional vibration modal of gas turbine pull-rod type rotor
A verification method and technology of pulling rod rotors, which are applied in computing, special data processing applications, instruments, etc., can solve the problems of rotor dynamic performance calculation errors, reduce the accuracy of rotor systems, and generate resonance.
- Summary
- Abstract
- Description
- Claims
- Application Information
AI Technical Summary
Problems solved by technology
Method used
Image
Examples
Embodiment Construction
[0032] An embodiment of the present invention is: the structure of the contact section of the experimental rod rotor is as follows figure 1 As shown, the rotor has 7 identical contact segments. The surface profile curve of the contact surface of the rotor disc is as follows: figure 2 As shown, it is the mean square value σ of the asperity height of the contact surface of the wheel disk measured by the SG201P surface topography instrument m 0.96μm, the average radius of curvature R s is 290 μm, and the asperity distribution density is 7.11×10 7 / m 2 . Modulus of elasticity of wheel material E 0 2.06×10 11 Pa, the equivalent elastic modulus E is 1.132×10 11 Pa, Poisson's ratio ν is 0.3, and the maximum coefficient of static friction is μ is 0.2.
[0033] A method for calculating and verifying the torsional vibration mode of a tie-rod rotor of a gas turbine comprises the following steps:
[0034] 1. Establish the transfer matrix equation of the tie rod rotor contact sec...
PUM
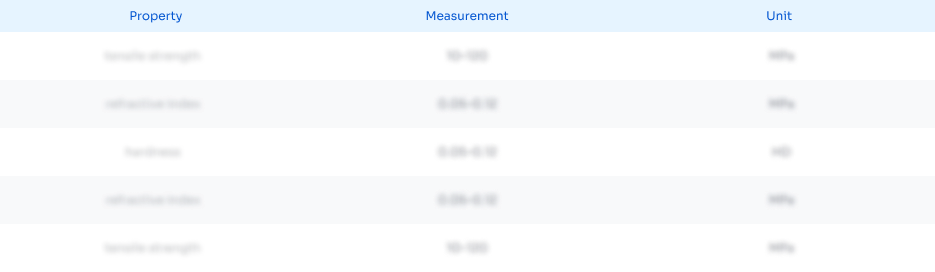
Abstract
Description
Claims
Application Information

- R&D Engineer
- R&D Manager
- IP Professional
- Industry Leading Data Capabilities
- Powerful AI technology
- Patent DNA Extraction
Browse by: Latest US Patents, China's latest patents, Technical Efficacy Thesaurus, Application Domain, Technology Topic, Popular Technical Reports.
© 2024 PatSnap. All rights reserved.Legal|Privacy policy|Modern Slavery Act Transparency Statement|Sitemap|About US| Contact US: help@patsnap.com