Foam concrete preform release agent and preparation method thereof
A foamed concrete and a production method technology, applied in the petroleum industry, lubricating compositions, etc., can solve problems such as unfavorable secondary construction, surface oil stains, edge defects, etc., and achieve smooth demoulding, no oil stain on the surface, and neat edges and corners without defects. Effect
- Summary
- Abstract
- Description
- Claims
- Application Information
AI Technical Summary
Problems solved by technology
Method used
Image
Examples
Embodiment Construction
[0016] One, the composition and the weight percent of the special high-efficiency release agent for foamed concrete prefabricated parts of the present invention are respectively:
[0017]
[0018] Second, the specific preparation steps:
[0019] 1. First put stearic acid into the pot and heat to melt, set aside;
[0020] 2. Add caustic soda into the reaction kettle according to the formula amount, and dissolve caustic soda under constant stirring;
[0021] 3. Slowly add the melted stearic acid into the lye in the reaction kettle and stir quickly evenly, heat up to 50-60°C to make soap liquid;
[0022] 4. When the temperature of the soap liquid in the reaction kettle is cooled below 50°C, add OP-10 emulsifier, talcum powder, and phosphoric acid and stir evenly. At this temperature, continuously add waste engine oil and stir vigorously to emulsify it completely. Continue to stir for 30-40 minutes, and then the material can be cooled and discharged;
[0023] Release agent c...
PUM
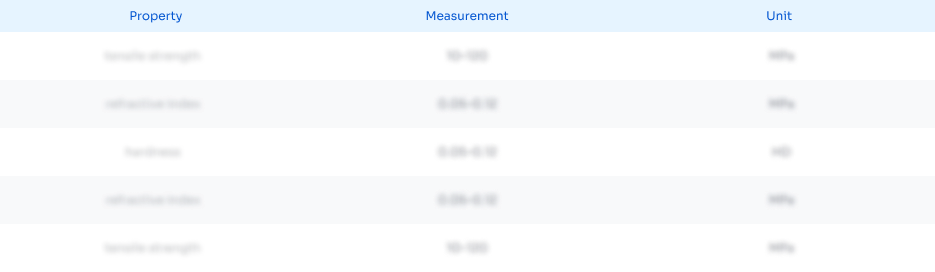
Abstract
Description
Claims
Application Information

- Generate Ideas
- Intellectual Property
- Life Sciences
- Materials
- Tech Scout
- Unparalleled Data Quality
- Higher Quality Content
- 60% Fewer Hallucinations
Browse by: Latest US Patents, China's latest patents, Technical Efficacy Thesaurus, Application Domain, Technology Topic, Popular Technical Reports.
© 2025 PatSnap. All rights reserved.Legal|Privacy policy|Modern Slavery Act Transparency Statement|Sitemap|About US| Contact US: help@patsnap.com