ERG (exhaust gas recirculation) mixer
A mixer and cavity technology, which is used in machines/engines, adding non-fuel substances to fuel, internal combustion piston engines, etc., can solve the problem that the mixing uniformity of recirculated exhaust gas can no longer meet the requirements of stable operation of the engine, and the intake pipeline is short. and other problems, to achieve the effect of improving mixing uniformity and mixing efficiency, compact structure and cost saving
- Summary
- Abstract
- Description
- Claims
- Application Information
AI Technical Summary
Problems solved by technology
Method used
Image
Examples
Embodiment 1
[0019] Such as figure 1 , 3 As shown, the EGR mixer of this embodiment includes a second cavity 5 and a straight cylindrical first cavity 6, the first cavity 6 includes a first air inlet 2 and an air outlet 3, and the second cavity 5 includes a first Two air inlets 1, the second cavity 5 communicate with the inside of the first cavity 6 through a plurality of ventilation holes 4 on the wall of the first cavity 6, and the ventilation holes 4 are distributed in the first cavity 6 in a ring shape Around the wall of the cavity to improve the mixing uniformity of fresh air and EGR exhaust gas; the second cavity 5 is provided with an intake pipe 9 facing the wall of the first cavity 6, and the second air inlet 1 is arranged at the end of the intake pipe 9 part, and is provided with a connecting flange 7.
[0020] Such as figure 2 As shown, the vent hole 4 is provided with a guide tube 8 towards the inside of the first cavity 6, so that the gas entering the first cavity 6 through...
PUM
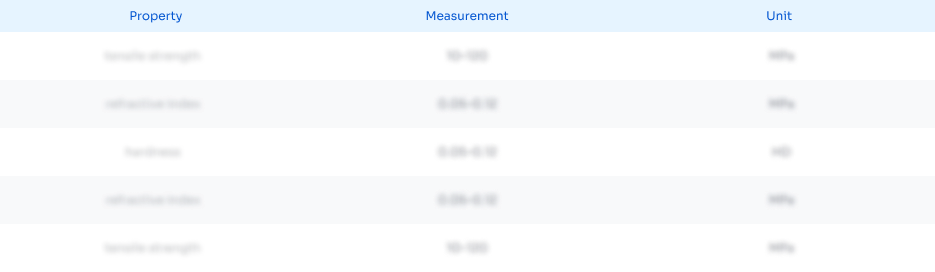
Abstract
Description
Claims
Application Information

- R&D Engineer
- R&D Manager
- IP Professional
- Industry Leading Data Capabilities
- Powerful AI technology
- Patent DNA Extraction
Browse by: Latest US Patents, China's latest patents, Technical Efficacy Thesaurus, Application Domain, Technology Topic, Popular Technical Reports.
© 2024 PatSnap. All rights reserved.Legal|Privacy policy|Modern Slavery Act Transparency Statement|Sitemap|About US| Contact US: help@patsnap.com