Method for increasing yield of rectisol and/or liquid oxygen wash greatly and saving energy through pressure swing adsorption technique and device thereof
A low-temperature methanol washing and pressure swing adsorption technology, which is applied in hydrogen production, sustainable manufacturing/processing, chemical industry, etc., can solve the problems of difficult transformation, many equipment, and infeasible transformation, so as to increase the burden of environmental emissions and avoid The effect of large investment and increased emissions
- Summary
- Abstract
- Description
- Claims
- Application Information
AI Technical Summary
Problems solved by technology
Method used
Image
Examples
Embodiment 1
[0035] This embodiment is an example of production increase and energy-saving modification of Lurgi furnace or BGL furnace coal gas-to-ammonia synthesis device. The block diagram of the process is shown in figure 1 .
[0036] This embodiment is realized by the following scheme. The conditions for changing gas before transformation are: flow rate (dry): 120975Nm3 / h, temperature: 37°C, pressure: 2.65MPa(A)
[0037] Composition: mol%
[0038] CO2 37.69
[0039] H2S+COS 0.06
[0040] CO 4.79
[0041] H2 48.61
[0042] CH4 6.79
[0043] C2H6 0.4
[0044] N2 1.13
[0045] AR 0.53.
[0046] The above-mentioned shift gas from the sulfur-resistant shift, after heat recovery, condensation cooling and separation of the condensate, first enters the low-temperature methanol desulfurization device 100 for desulfurization, and then the desulfurization gas 110 is divided into two streams, and one stream 111 is reheated and then transformed into pressure The adsorption decarbonization...
Embodiment 2
[0052] This embodiment is an example of production increase and energy-saving transformation of a coal-water slurry coal gas-to-gas synthesis ammonia plant. The flow block diagram is shown in the appendix figure 2 .
[0053] This embodiment is realized by the following scheme. The conditions for changing gas before transformation are: flow rate (dry): 152323Nm3 / h, temperature: 40°C, pressure: 5.58MPa(A)
[0054] Composition: mol%
[0055] CO2 43.17
[0056] H2S+COS 0.29
[0057] CO 1.50
[0058] H2 54.53
[0059] CH4 0.07
[0060] N2 0.35
[0061] AR 0.09
[0062] The above-mentioned shift gas from the sulfur-resistant shift, after heat recovery, condensation cooling and separation of the condensate, first enters the low-temperature methanol desulfurization device 100 for desulfurization, and then the desulfurization gas 110 is divided into two streams, and one stream 111 is reheated and then transformed into pressure The adsorption decarbonization device 200 performs...
Embodiment 3
[0068] This embodiment is an example of coal gas production based on the production increase and energy-saving transformation of the residual oil gas production ammonia synthesis device. The flow block diagram is shown in the appendix image 3 .
[0069] This embodiment is realized by the following scheme. The conditions for changing gas before transformation are: flow rate (dry): 80000Nm3 / h, temperature: 45°C, pressure: 5.52MPa(A)
[0070] Composition: mol%
[0071] CO2 2.95
[0072] H2S+COS 0.29
[0073] CO 47.90
[0074] H2 48.13
[0075] CH4 0.27
[0076] N2 0.10
[0077] AR 0.36
[0078] The above reformed gas from non-catalytic partial oxidation, after heat recovery, condensation and cooling and separation of condensate, first enters the low-temperature methanol desulfurization device 100 for desulfurization, then passes through the saturation tower and adds steam, and then enters the CO conversion device 800 to convert CO into H2, shift gas 810 is divided into t...
PUM
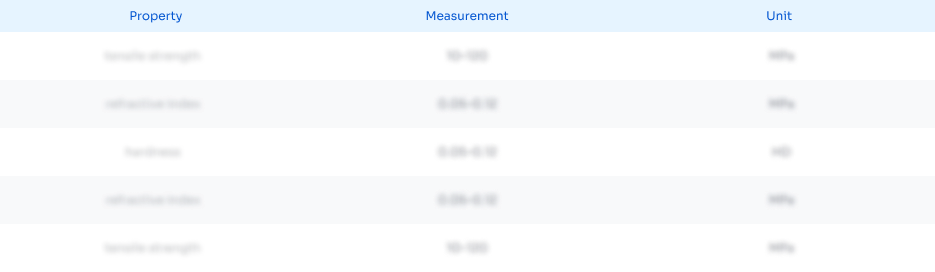
Abstract
Description
Claims
Application Information

- R&D
- Intellectual Property
- Life Sciences
- Materials
- Tech Scout
- Unparalleled Data Quality
- Higher Quality Content
- 60% Fewer Hallucinations
Browse by: Latest US Patents, China's latest patents, Technical Efficacy Thesaurus, Application Domain, Technology Topic, Popular Technical Reports.
© 2025 PatSnap. All rights reserved.Legal|Privacy policy|Modern Slavery Act Transparency Statement|Sitemap|About US| Contact US: help@patsnap.com