Diversion method for composite vacuum perfusion molding process
A composite material and vacuum infusion technology, applied in the field of composite material molding technology, can solve the problems of loss of liquid resin, long molding time, low production efficiency, etc., and achieve the effects of improving compression resistance, shortening molding time, and improving production efficiency
- Summary
- Abstract
- Description
- Claims
- Application Information
AI Technical Summary
Problems solved by technology
Method used
Image
Examples
Embodiment 1
[0020] An application example of vacuum infusion molding of large composite wind turbine blades with a length of 50 m and a width of 5 m.
[0021] The 50m wind power blade is divided into upper and lower shells, which are formed by vacuum infusion during molding. After curing, the upper and lower shells are bonded together with adhesive. The layering method of the upper and lower shells is exactly the same as the layering structure, and any of them can be called a half shell.
[0022] When the half-shell is being formed, 3 layers of dry fiber layers are laid on the entire surface of the half-shell forming mold along the length direction from 10m to 50m, and the main composite material prefabricated by unidirectional glass fiber is laid along the length direction from 10m to 50m. Beam, the main beam is located in the center of the width direction of the forming mold, the honeycomb sandwich material with the same height as the main beam is laid on both sides of the main beam, an...
Embodiment 2
[0025] An application example of vacuum infusion molding of large composite wind turbine blades with a length of 50m and a width of 5m.
[0026] The 50m wind power blade is divided into upper and lower shells, which are formed by vacuum infusion during molding. After curing, the upper and lower shells are bonded together with adhesive. The layering method of the upper and lower shells is exactly the same as the layering structure, and any of them can be called a half shell.
[0027] When the half-shell is being formed, 100 layers of dry fiber layers are laid on the entire surface of the molding die of the lower shell along the length direction from 0m to 10m.
[0028] Then lay two diversion media along the width direction on the upper surface of the above-mentioned dry laying layer. The diversion medium is composed of a space mesh fabric with a certain thickness. Its function is that during vacuum infusion molding, the liquid resin can quickly disperse into these space mesh s...
PUM
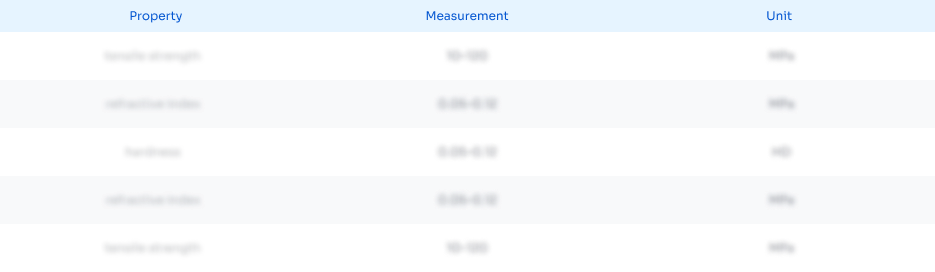
Abstract
Description
Claims
Application Information

- Generate Ideas
- Intellectual Property
- Life Sciences
- Materials
- Tech Scout
- Unparalleled Data Quality
- Higher Quality Content
- 60% Fewer Hallucinations
Browse by: Latest US Patents, China's latest patents, Technical Efficacy Thesaurus, Application Domain, Technology Topic, Popular Technical Reports.
© 2025 PatSnap. All rights reserved.Legal|Privacy policy|Modern Slavery Act Transparency Statement|Sitemap|About US| Contact US: help@patsnap.com