Hydrocarbon oil cracking method for reducing sulfur content of gasoline
A sulfur content, gasoline technology, applied in cracking, catalytic cracking, petroleum industry, etc., can solve the problems of high cost of desulfurization cracking catalyst, increase olefin yield, etc., achieve low price, increase olefin yield, reduce gasoline sulfur content Effect
- Summary
- Abstract
- Description
- Claims
- Application Information
AI Technical Summary
Problems solved by technology
Method used
Image
Examples
Embodiment 1
[0030] In this example, a black vanadium ore K-B with low vanadium content is used as the desulfurization active component of the catalyst, and its characteristic chemical composition is 14.6Al 2 o 3 ●50.2SiO2 2 ●3.6V 2 o 5 ●10.4Fe 2 o 3 ●3.5P 2 o 5 8.6K 2O ● 2.2MgO ● 2.2CaO ● 2.0BaO, the vanadium ore is composed of 47% quartz, 8.9% feldspar and 44.1% clay minerals, and its diffraction spectrum is shown in the figure. Vanadium ore needs to be ground into powder by ball mill before use.
[0031] Pseudo-boehmite (solid content 61.7% by weight, produced by Shandong Aluminum Plant) was added into deionized water, and after stirring for 30 minutes, adding concentration of 36% hydrochloric acid (chemically pure, produced by Beijing Chemical Plant) was acidified, and the aluminum The ratio is controlled at 0.15-0.2. At this time, the pH value of the slurry is about 1.0-1.5. After stirring at room temperature for 1 hour, the temperature is raised to 65°C and then statically a...
Embodiment 2
[0036] Vanadium ore used in the present embodiment is the same as embodiment 1.
[0037] The preparation process of the desulfurization composition is the same as that in Example 1, the difference lies in the content of kaolin and vanadium ore, and the desulfurization composition Z-2 is obtained.
[0038] The composition of composition Z-2 is: 35% by weight of REHY molecular sieve, 25% by weight of kaolin, 10% by weight of aluminum sol, 20% by weight of pseudo-boehmite, and 10% by weight of K-B.
[0039] The cracking reaction conditions are the same as in Example 1, and the cracking evaluation results are shown in Table 2.
Embodiment 3
[0041] Vanadium ore used in the present embodiment is the same as embodiment 1.
[0042] The preparation process of the desulfurization composition is the same as that in Example 1, the difference lies in the content of kaolin and vanadium ore, and the desulfurization composition Z-3 is obtained.
[0043] The composition of composition Z-3 is: 35% by weight of REHY molecular sieve, 20% by weight of kaolin, 10% by weight of aluminum sol, 20% by weight of pseudo-boehmite, and 15% by weight of K-B.
[0044] The cracking reaction conditions are the same as in Example 1, and the cracking evaluation results are shown in Table 2.
PUM
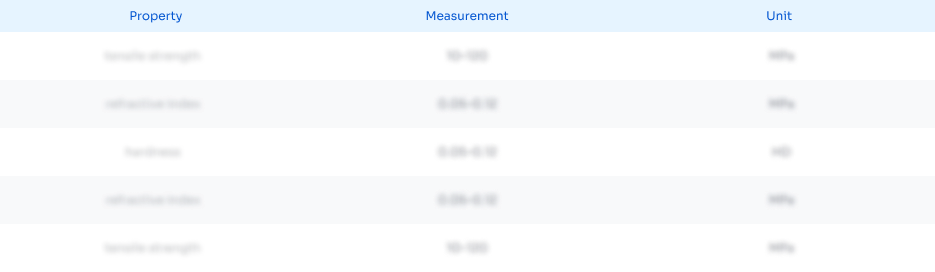
Abstract
Description
Claims
Application Information

- R&D
- Intellectual Property
- Life Sciences
- Materials
- Tech Scout
- Unparalleled Data Quality
- Higher Quality Content
- 60% Fewer Hallucinations
Browse by: Latest US Patents, China's latest patents, Technical Efficacy Thesaurus, Application Domain, Technology Topic, Popular Technical Reports.
© 2025 PatSnap. All rights reserved.Legal|Privacy policy|Modern Slavery Act Transparency Statement|Sitemap|About US| Contact US: help@patsnap.com