Flame correcting method for rudder horn shell plate
A technology of flame straightening and shell plate, applied in the field of flame straightening, which can solve the problems of increasing the straightening work cycle, cost, and poor straightening effect, and achieves the effects of high straightening efficiency, reduced procedures, and low straightening cost
- Summary
- Abstract
- Description
- Claims
- Application Information
AI Technical Summary
Problems solved by technology
Method used
Image
Examples
Embodiment Construction
[0014] Such as figure 1 As shown, in the flame correction method of the rudder arm shell plate of the present invention, firstly, the cold-worked rudder arm shell plate 1 is reversed, and its four corners are placed on four pads 2 of the same height. The pad 2 can be an iron block or a square wood pad. Due to the longitudinal and twisting deformation of the rudder arm shell plate 1 after cold working, the rudder arm shell plate 1 is naturally placed behind the pad 2, and the rudder arm The shell plate 1 will have one or a pair of corners and a certain gap 3 between the spacer block 2 (such as figure 1 Shown is the case where there is a gap between one corner and the spacer 2); then, according to the deformation position and amount of the rudder arm shell plate 1, a heating line 4 is drawn longitudinally on the rudder arm shell plate 1, and the other is Vertical pressure is applied to the upper surface of the rudder arm shell plate 1, so that the cold metal area has an addition...
PUM
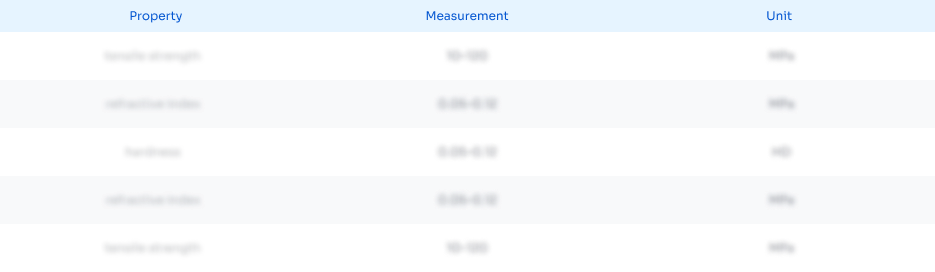
Abstract
Description
Claims
Application Information

- R&D
- Intellectual Property
- Life Sciences
- Materials
- Tech Scout
- Unparalleled Data Quality
- Higher Quality Content
- 60% Fewer Hallucinations
Browse by: Latest US Patents, China's latest patents, Technical Efficacy Thesaurus, Application Domain, Technology Topic, Popular Technical Reports.
© 2025 PatSnap. All rights reserved.Legal|Privacy policy|Modern Slavery Act Transparency Statement|Sitemap|About US| Contact US: help@patsnap.com