Double-faced uniform forming method of gypsum plaster ceiling board
A molding method and ceiling technology, applied in the direction of supply devices, manufacturing tools, etc., can solve the problems of mass production of high-quality gypsum ceilings, poor surface quality, and unsatisfactory requirements
- Summary
- Abstract
- Description
- Claims
- Application Information
AI Technical Summary
Problems solved by technology
Method used
Image
Examples
Embodiment
[0020] 1-soft mold for the inner surface of the upper mold, 2-outer mold for the upper mold, 3-outer mold for the lower mold, 4-soft mold for the inner surface of the lower mold, 5-flash groove, 6-gypsum slurry, 7-formed gypsum ceiling
[0021] Such as figure 1 As shown, the outer formwork 2 of the upper mold and the outer mold 3 of the lower mold in the figure are all made of hard materials (aluminum alloy), which are convenient for fixing and moving; 1 and 4 are soft molds made of polymer materials, which are respectively attached to the outer formwork 2. There is a fixed connection between the soft mold and the hard mold on the inner surface. The specific manufacturing process is as follows: ① upper mold grouting: inject an appropriate amount of gypsum slurry 6 into the upper mold 1, spread the gypsum slurry evenly in the upper mold 1, and vibrate to form evenly. ② Grouting of the lower mold: After the gypsum slurry of the upper mold is dry to a certain extent, the gypsum ...
PUM
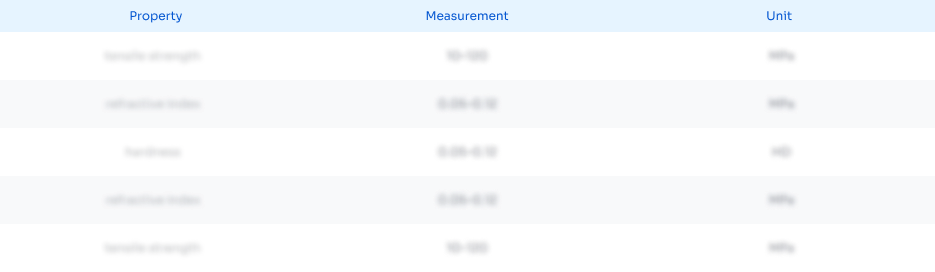
Abstract
Description
Claims
Application Information

- R&D
- Intellectual Property
- Life Sciences
- Materials
- Tech Scout
- Unparalleled Data Quality
- Higher Quality Content
- 60% Fewer Hallucinations
Browse by: Latest US Patents, China's latest patents, Technical Efficacy Thesaurus, Application Domain, Technology Topic, Popular Technical Reports.
© 2025 PatSnap. All rights reserved.Legal|Privacy policy|Modern Slavery Act Transparency Statement|Sitemap|About US| Contact US: help@patsnap.com