Method for preparing high-efficiency modified asphalt
A modified asphalt, high-efficiency technology, applied in textiles and papermaking, building components, fiber chemical characteristics, etc., can solve the problems of high energy consumption and long time consumption, and achieve simple preparation process, short time consumption and high product softening point Effect
- Summary
- Abstract
- Description
- Claims
- Application Information
AI Technical Summary
Problems solved by technology
Method used
Examples
Embodiment 1
[0024] Add petroleum asphalt with a carbon content of more than 50%, modifier, and potassium permanganate into the reactor at a weight ratio of 100:5:5, and heat the reactor to 200°C to prepare molten asphalt; Add the prepared molten asphalt into the atomizing and tempering tower with a temperature of 400°C, atomize and temper the molten asphalt for 3 hours; then input the atomized and tempered molten asphalt into the emulsification device at a temperature of 250°C and adding an emulsifier accounting for 5% by mass of the amount of asphalt for emulsification and conditioning; after emulsification and conditioning, cool down to below 230°C and discharge to obtain high-efficiency asphalt.
Embodiment 2
[0026] Add petroleum asphalt with a carbon content of more than 50%, modifier, and potassium nitrate into the reactor at a weight ratio of 100:7:5, and heat the reactor to 230°C to prepare molten asphalt; The good molten asphalt is added to the atomizing and tempering tower with a temperature of 380°C, and the molten asphalt is atomized and tempered for 4.5 hours; then the atomized and tempered molten asphalt is input into the emulsification device at a temperature of 300°C, And add an emulsifier accounting for 7% of the amount of asphalt by mass for emulsification and conditioning; after emulsification and conditioning, cool down to below 200°C and discharge to obtain high-efficiency asphalt.
Embodiment 3
[0028] Put the asphalt, modifier and naphthalene obtained by thermal condensation polymerization of petroleum residue with a carbon content of more than 50% into the reactor at a weight ratio of 100:5:7, and heat the reactor to 250°C. Prepare molten asphalt; add the prepared molten asphalt to the atomization conditioning tower with a temperature of 430°C, atomize and condition the molten asphalt for 4 hours; then input the atomized and tempered molten asphalt into the ℃, and add an emulsifier accounting for 10% by mass of the asphalt to carry out emulsification and conditioning; after emulsification and conditioning, cool down to below 200 ℃ and discharge to obtain high-efficiency asphalt.
PUM
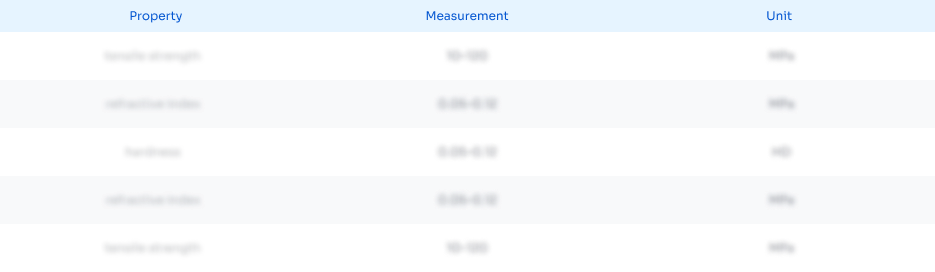
Abstract
Description
Claims
Application Information

- R&D
- Intellectual Property
- Life Sciences
- Materials
- Tech Scout
- Unparalleled Data Quality
- Higher Quality Content
- 60% Fewer Hallucinations
Browse by: Latest US Patents, China's latest patents, Technical Efficacy Thesaurus, Application Domain, Technology Topic, Popular Technical Reports.
© 2025 PatSnap. All rights reserved.Legal|Privacy policy|Modern Slavery Act Transparency Statement|Sitemap|About US| Contact US: help@patsnap.com