Correction method for multi-point measurement of steam drum liquid level of high pressure boiler
A steam drum liquid level and multi-point measurement technology, which is applied in the direction of liquid/fluid solid measurement, measuring devices, liquid level indicators, etc., can solve the problem of affecting the control of the steam drum liquid level, large deviation of liquid level measurement, and inability to guarantee Problems such as the accuracy and consistency of multi-point liquid level measurement values, to achieve the effect of eliminating system errors, solving difficulties in accuracy and consistency, and ensuring consistency
- Summary
- Abstract
- Description
- Claims
- Application Information
AI Technical Summary
Problems solved by technology
Method used
Image
Examples
Embodiment Construction
[0022] Due to installation reasons, the h of each pressure taking device 1 and h 2 It's all different. refer to figure 1 Measure and record the installation position of the liquid level measuring device 2, after measurement, the height h between the two connecting ports of the liquid level measuring device 2 and the steam drum 1 1 =700mm, the height h between the liquid level measuring device 2 and the lower connection port of the steam drum 1 to the differential pressure transmitter 3 2 =250mm.
[0023] According to the working conditions, determine the saturated water density ρ in the steam drum 1 液 =675.3kg / m 3 , saturated steam density ρ 汽 =60.94kg / m 3 , and the condensate density ρ in the liquid level measuring device 2 冷 =915.8kg / m 3 ; The pressure P in the steam drum 1 and the liquid level measuring device 2 1 = 11.0 MPa.
[0024] Calculate the range ΔP and migration P of the differential pressure transmitter 3 of the liquid level measuring device 2:
[0025...
PUM
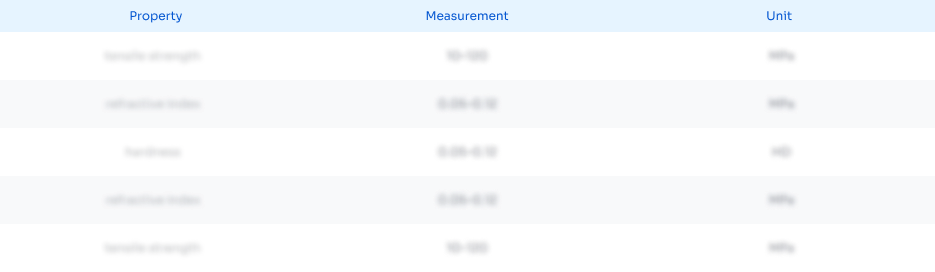
Abstract
Description
Claims
Application Information

- R&D
- Intellectual Property
- Life Sciences
- Materials
- Tech Scout
- Unparalleled Data Quality
- Higher Quality Content
- 60% Fewer Hallucinations
Browse by: Latest US Patents, China's latest patents, Technical Efficacy Thesaurus, Application Domain, Technology Topic, Popular Technical Reports.
© 2025 PatSnap. All rights reserved.Legal|Privacy policy|Modern Slavery Act Transparency Statement|Sitemap|About US| Contact US: help@patsnap.com