Aluminium alloy, core support prepared by same for forming of aluminum alloy casting and preparation of core support
A technology for aluminum alloy castings and aluminum alloys, which is used in casting molding equipment, metal processing equipment, casting molds, etc., can solve the problems of poor fusion of core support and aluminum alloy casting body, inability to meet pressure requirements, and lack of densification. Achieve the effect of avoiding the generation of stratified cold insulation, overcoming the effect of surface tension, and meeting internal quality requirements
- Summary
- Abstract
- Description
- Claims
- Application Information
AI Technical Summary
Problems solved by technology
Method used
Image
Examples
Embodiment 1
[0022] This embodiment is an example of applying the content of the present invention to casting a pressure-bearing aluminum alloy casting for aviation. The material of the casting is ZL101, the pouring temperature is 710°C, the inner cavity is required to bear pressure, and the wall thickness of the pressure-bearing cavity is 5mm. This example needs to be 5mm (length) * 5mm (width) * 2mm (thickness) with the core support side wall size, comb support plate size is 4mm (length) * 4mm (width) * 2mm (thickness). The alloy composition is prepared according to Si is 11.8 (wt)%, Mg is 0.22 (wt)%, Al is 87.98 (wt)%, wherein Mg is added through Al-Mg master alloy, melted in an induction furnace, and poured into a square A square alloy ingot is obtained in a graphite ingot mold. After the alloy ingot is annealed, it is blanked according to the required size of the support, and the aluminum alloy support required in this example is manufactured according to the structure of the support ...
Embodiment 2
[0024] This embodiment is an example of applying the content of the present invention to casting a pressure-bearing aluminum alloy casting for aviation. The material of the casting is ZL105A, the pouring temperature is 720°C, the inner cavity is required to bear pressure, and the wall thickness of the pressure-bearing cavity is 7mm. In this example, the size of the core support side wall is 7mm (length) × 7mm (width) × 2mm (thickness), the size of the comb support plate is 6mm (length) × 6mm (width) × 2mm (thickness), and the width of the comb gap is 1mm. There are 3 items in total. The alloy composition is formulated according to 12.5(wt)% of Si, 0.28(wt)% of Mg, and 87.22(wt)% of Al, wherein Mg is added through Al-Mg master alloy, melted in an induction furnace, and poured into a square A square alloy ingot is obtained in a graphite ingot mold. After the alloy ingot is annealed, it is blanked according to the required size of the support, and the aluminum alloy support requ...
PUM
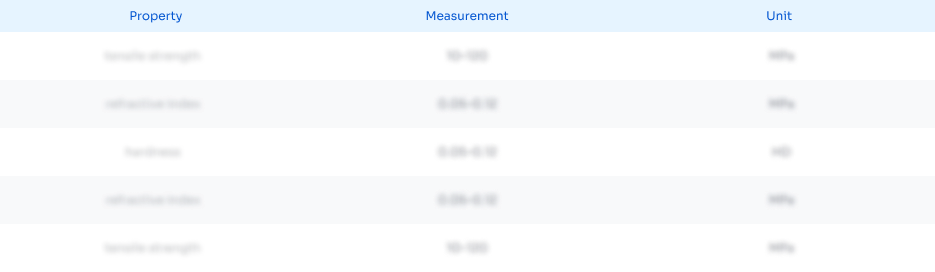
Abstract
Description
Claims
Application Information

- R&D
- Intellectual Property
- Life Sciences
- Materials
- Tech Scout
- Unparalleled Data Quality
- Higher Quality Content
- 60% Fewer Hallucinations
Browse by: Latest US Patents, China's latest patents, Technical Efficacy Thesaurus, Application Domain, Technology Topic, Popular Technical Reports.
© 2025 PatSnap. All rights reserved.Legal|Privacy policy|Modern Slavery Act Transparency Statement|Sitemap|About US| Contact US: help@patsnap.com