Method for connecting electrolytic aluminum anode without pouring
A technology of electrolytic aluminum anode and connection method, applied in the field of pour-free connection of electrolytic aluminum anode, can solve the problems of increasing the voltage drop of the conductive device, increasing the energy consumption, high labor intensity, etc., so as to increase the conductive contact area and reduce the conductive The effect of voltage drop and labor intensity reduction
- Summary
- Abstract
- Description
- Claims
- Application Information
AI Technical Summary
Problems solved by technology
Method used
Image
Examples
Embodiment Construction
[0010] as attached figure 2 As shown, the cross section of the steel claw 1 is made into a wedge shape with a large bottom and a small top, and the wedge shape is asymmetrical. The angle on the left is 1.5°, and the angle on the right is 3°. The anode carbon block 2 is made into a boss shape in cross section. In the middle of the upper plane, a dovetail-shaped through groove 8 is opened longitudinally. The angle of the two side walls of the dovetail-shaped through-groove 8 is equal to the side with the smaller angle of the steel claw. The cross-section of the dovetail-shaped through-groove 8 is larger than that of the steel claw 1. After the steel claw 1 is put into the dovetail-shaped through groove 8, three copper plates 4 with the same thickness are correspondingly put into the gaps on both sides of the steel claw 1 (as attached figure 1 As shown), on the side of the steel claw 1 with a larger angle, a stainless steel wedge plate 5 with the same angle as the gap is filled ...
PUM
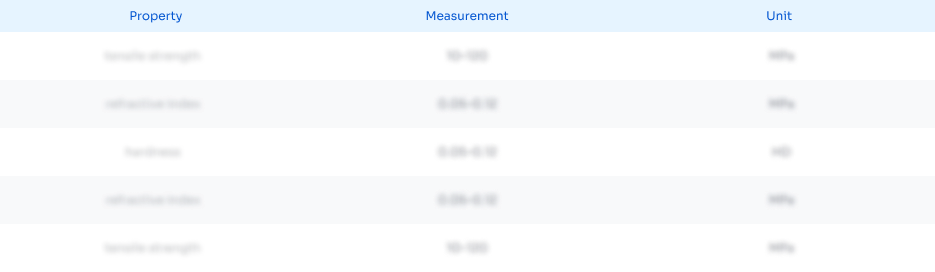
Abstract
Description
Claims
Application Information

- R&D
- Intellectual Property
- Life Sciences
- Materials
- Tech Scout
- Unparalleled Data Quality
- Higher Quality Content
- 60% Fewer Hallucinations
Browse by: Latest US Patents, China's latest patents, Technical Efficacy Thesaurus, Application Domain, Technology Topic, Popular Technical Reports.
© 2025 PatSnap. All rights reserved.Legal|Privacy policy|Modern Slavery Act Transparency Statement|Sitemap|About US| Contact US: help@patsnap.com