Prefabricated reinforced concrete beam and connection joint of reinforced concrete column and beam
A technology for reinforced concrete beams and connecting nodes, which is applied to structural elements, building components, and elongated structural components used for load-bearing, etc., and can solve the problem of insufficient integrity, bending resistance, shear resistance, and torsional strength of beam-column connection nodes , It is impossible to design problems such as prestressed tension, compression resistance, and shear resistance, so as to improve earthquake resistance and safety, reduce construction waste pollution, and ensure quality.
- Summary
- Abstract
- Description
- Claims
- Application Information
AI Technical Summary
Problems solved by technology
Method used
Image
Examples
Embodiment 1
[0027] Embodiment 1: see figure 1 , The prefabricated reinforced concrete beam of the present invention includes the outer concrete 1, the inner reinforcement cage 2 designed according to the load, and the connecting steel joints at both ends. The shaped steel joints are transverse T-shaped steel, the section of the T-shaped end plate 4 is slightly smaller than the end face of the reinforced concrete beam, and shrinks in the inner end face of the reinforced concrete beam. The end plate has through holes corresponding to the main and auxiliary steel bars in each axial direction. The plate 4 forms a perforated plug welding connection, and the T-shaped handle is composed of an upper and lower horizontal plate 6 and a middle vertical plate 5 to form an I-shaped (H-shaped) structure connection portion, and the vertical plate 5 has a connection hole. There are short shear parts 7 inside the reinforced concrete on the end face of the T-shaped connecting steel, and a rigid steel membe...
Embodiment 2
[0028]Example 2: see figure 2 , As in Example 1, there are prestressed tension holes on the lower side of the reinforced concrete beam section axially (including through the T-shaped end plate 4), and built-in prestressed tension steel bars 8. This structural beam, one can reduce the beam section under the same load, and the other can be used for beams with a span greater than 8 meters.
Embodiment 3
[0029] Embodiment 3: see image 3 , the connection node between the reinforced concrete column and the beam, including the reinforced concrete column 9 made of steel bars or steel pipes, in the area where it is connected to the beam, there is a built-in rigid steel pipe 10, and the steel pipe radially has a shear member (not shown in the figure) extending out, One side or two sides or three sides or four sides each have radially protruding I-shaped connecting section steel 11 with the same shape as the aforementioned beam connection part. After connecting with the beam, fill the package with concrete.
PUM
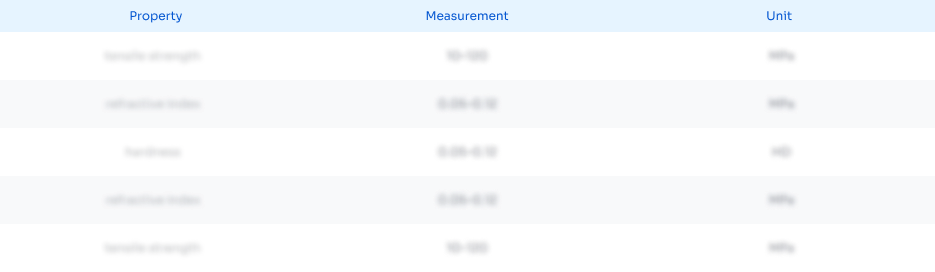
Abstract
Description
Claims
Application Information

- Generate Ideas
- Intellectual Property
- Life Sciences
- Materials
- Tech Scout
- Unparalleled Data Quality
- Higher Quality Content
- 60% Fewer Hallucinations
Browse by: Latest US Patents, China's latest patents, Technical Efficacy Thesaurus, Application Domain, Technology Topic, Popular Technical Reports.
© 2025 PatSnap. All rights reserved.Legal|Privacy policy|Modern Slavery Act Transparency Statement|Sitemap|About US| Contact US: help@patsnap.com