Method for removing vanadium from titanium tetrachloride
A technology of titanium tetrachloride and mixed liquid, applied in the direction of titanium halide, etc., can solve the problems of poor control of material temperature, high production cost, unsuitable configuration of electric heating device, etc., achieve stable temperature control and solve the effect of short life
- Summary
- Abstract
- Description
- Claims
- Application Information
AI Technical Summary
Problems solved by technology
Method used
Image
Examples
Embodiment Construction
[0020] see figure 1 The flow process of the method for removing vanadium from titanium tetrachloride of the present invention is described in more detail. Before device startup, in AlCl 3 Preparation of AlCl in the mixed solution preparation tank 3 Mixed solution, AlCl in mixed solution 3 and crude TiCl 4 The weight ratio of AlCl is 1:7, as a catalyst for vanadium removal reaction, AlCl 3 The solubility is low, use 0.6-0.7MPa water vapor to heat and insulate the materials in the aluminum trichloride preparation tank; prepare the aluminum powder mixture, aluminum powder and coarse TiCl in the aluminum powder mixture preparation tank 4 The weight ratio of AlCl is 1:82, the prepared AlCl 3 The mixed liquid and the aluminum powder mixed liquid are respectively continuously added to the vanadium removal reactor; at the same time, the cold crude titanium tetrachloride is continuously heated to 130-135°C by the start-up preheater and then enters the vanadium removal reactor. Th...
PUM
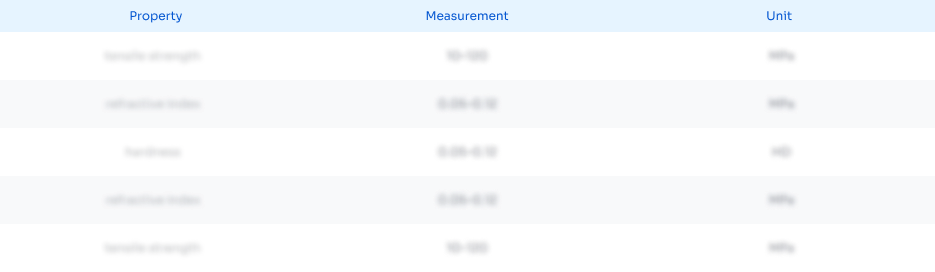
Abstract
Description
Claims
Application Information

- R&D
- Intellectual Property
- Life Sciences
- Materials
- Tech Scout
- Unparalleled Data Quality
- Higher Quality Content
- 60% Fewer Hallucinations
Browse by: Latest US Patents, China's latest patents, Technical Efficacy Thesaurus, Application Domain, Technology Topic, Popular Technical Reports.
© 2025 PatSnap. All rights reserved.Legal|Privacy policy|Modern Slavery Act Transparency Statement|Sitemap|About US| Contact US: help@patsnap.com