Linearly-driven four-degree of freedom hybrid mechanical arm
A linear drive, degree-of-freedom technology, used in manipulators, program-controlled manipulators, manufacturing tools, etc., can solve the problems of low speed, low positioning accuracy and repeatability, and small workspace/mechanism volume ratio. High repetitive positioning accuracy, high speed, and the effect of expanding the operating range
- Summary
- Abstract
- Description
- Claims
- Application Information
AI Technical Summary
Problems solved by technology
Method used
Image
Examples
Embodiment 1
[0019] Embodiment 1: as image 3 As shown, the linear drive four-degree-of-freedom hybrid manipulator of the present invention is used as a module, which is placed on the lead screw structure through a threaded connection structure to make it move in the horizontal direction.
Embodiment 2
[0020] Embodiment 2: as Figure 4 As shown, borrowing the principle of the traditional radial drilling machine, the linear drive four-degree-of-freedom hybrid manipulator of the present invention is fixed on the column so that it can rotate around the axis of the column.
Embodiment 3
[0021] Embodiment 3: as Figure 5 As shown, borrowing the principle of a vertical machine tool, the linear drive four-degree-of-freedom hybrid manipulator of the present invention is placed on the screw structure as a module to make it move vertically.
[0022] The linear-driven four-degree-of-freedom hybrid manipulator of the present invention is driven by a linear motor, and can realize motions with high speed, high positioning accuracy and repeatable positioning accuracy; , to effectively generate the advantageous feed direction or expand the working range, and overcome the shortcomings of the small working space and limited posture of the general parallel or series manipulator.
PUM
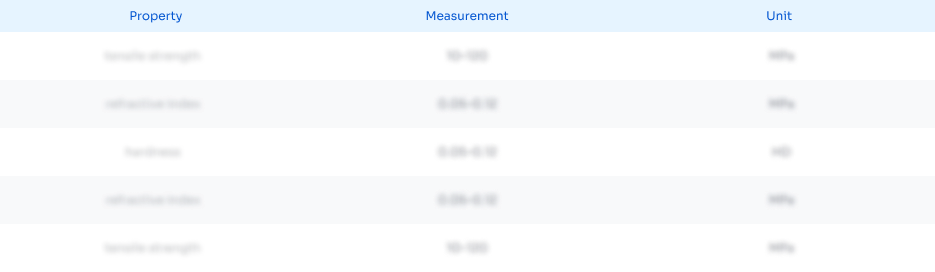
Abstract
Description
Claims
Application Information

- R&D
- Intellectual Property
- Life Sciences
- Materials
- Tech Scout
- Unparalleled Data Quality
- Higher Quality Content
- 60% Fewer Hallucinations
Browse by: Latest US Patents, China's latest patents, Technical Efficacy Thesaurus, Application Domain, Technology Topic, Popular Technical Reports.
© 2025 PatSnap. All rights reserved.Legal|Privacy policy|Modern Slavery Act Transparency Statement|Sitemap|About US| Contact US: help@patsnap.com