Control method for descending movable arm of excavator
A control method and technology of motorized arms, which are applied in the direction of mechanically driven excavators/dredgers, etc., can solve the problems of uncomfortable, strong shaking or shaking, and not very good for the operator of the excavator, and achieve a simple and convenient structure. Descent speed, easy to achieve effect
- Summary
- Abstract
- Description
- Claims
- Application Information
AI Technical Summary
Problems solved by technology
Method used
Image
Examples
Embodiment 1
[0016] Embodiment one: see figure 1 , 2 As shown, a control method for the lowering of the boom of the excavator uses the pilot pressure sensor installed in the hydraulic control circuit to detect the action of the operating handle. When the operating handle controls the lowering of the boom, the position sensor installed on the boom The position of the boom cylinder is detected, and the speed of the boom at this time is obtained through logical operation according to the position of the boom cylinder, the oil supply amount of the boom cylinder is controlled, and the lowering speed of the boom is controlled.
[0017] When using this method, take an excavator working on a construction site as an example. When the operator of the excavator pulls the handle of the boom, the controller collects signals from the pilot pressure sensor. If the pilot signal for lowering the boom is not collected, continue On the contrary, if the signal is collected, the controller will collect the si...
PUM
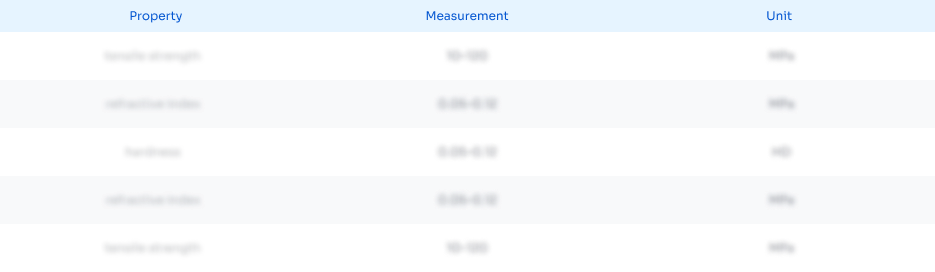
Abstract
Description
Claims
Application Information

- R&D Engineer
- R&D Manager
- IP Professional
- Industry Leading Data Capabilities
- Powerful AI technology
- Patent DNA Extraction
Browse by: Latest US Patents, China's latest patents, Technical Efficacy Thesaurus, Application Domain, Technology Topic, Popular Technical Reports.
© 2024 PatSnap. All rights reserved.Legal|Privacy policy|Modern Slavery Act Transparency Statement|Sitemap|About US| Contact US: help@patsnap.com