Method for manufacturing helical blade
A technology of a helical blade and a manufacturing method, which is applied to the manufacturing field of the helical blade, can solve the problems of cumbersome operation, low production efficiency, unable to form a positive helical surface, etc., and achieves the effect of improving work efficiency, avoiding cross operation and good forming effect.
- Summary
- Abstract
- Description
- Claims
- Application Information
AI Technical Summary
Problems solved by technology
Method used
Image
Examples
Embodiment Construction
[0032] Such as image 3 As shown, the manufacturing process of the spiral blade according to the present embodiment is as follows:
[0033] (1) Determine the position of the integral blade 1 and the mandrel 2: string the welded integral blade 1 with the inner hole on the mandrel 2, adjust the driving tapered roller 3 and the driven tapered roller 4, so that the two rollers clamp the whole At the starting end A end of the blade 1, the active tapered roller 3 can only rotate but cannot expand and contract in the axial direction. The driven tapered roller 4 can rotate under the drive of the driving tapered roller 3 . The driven tapered roller 4 is connected on a screw shaft 11 by a sliding bush, and the screw shaft 11 is threadedly connected with the fixing seat 12, so that the driven tapered roller 4 can rotate, the screw shaft 11 does not move, and the screw shaft 11 can only Axially moving along itself is realized by adjusting the tail end with a wrench, so that the driven t...
PUM
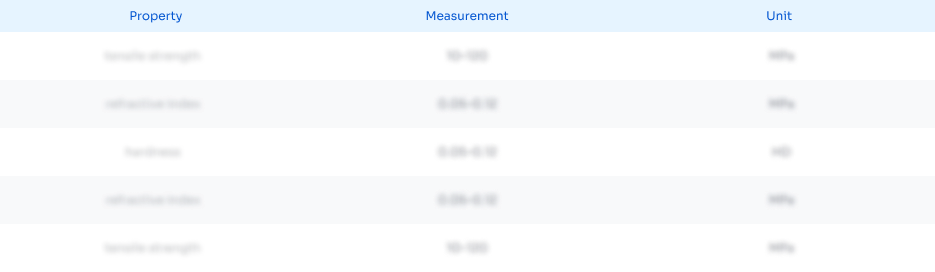
Abstract
Description
Claims
Application Information

- R&D
- Intellectual Property
- Life Sciences
- Materials
- Tech Scout
- Unparalleled Data Quality
- Higher Quality Content
- 60% Fewer Hallucinations
Browse by: Latest US Patents, China's latest patents, Technical Efficacy Thesaurus, Application Domain, Technology Topic, Popular Technical Reports.
© 2025 PatSnap. All rights reserved.Legal|Privacy policy|Modern Slavery Act Transparency Statement|Sitemap|About US| Contact US: help@patsnap.com