Catalytic conversion method for improving cetane number and yield of diesel
A catalytic conversion method and a technology for cetane number, applied in the field of catalytic conversion, can solve the problems of not mentioning improvement of diesel properties, low cetane number of light diesel oil, etc., and achieve performance improvement, catalyst content reduction, and crushing tendency reduction. Effect
- Summary
- Abstract
- Description
- Claims
- Application Information
AI Technical Summary
Problems solved by technology
Method used
Image
Examples
Embodiment 1
[0048] This example illustrates the use of the method provided by the present invention for selective cracking reaction to produce high-quality diesel.
[0049] The flow chart of the medium-sized catalytic cracking unit is shown in the figure. The feed oil is injected into the reaction zone I of the riser reactor through the pipeline 3, and it contacts and reacts with the catalyst A raised by the steam in the lower part of the riser reactor, and reacts in the riser. The weight ratio of catalyst A and feedstock oil in the vessel is 3:1, the residence time of feedstock oil in the riser reactor is 1.6 seconds, and the reaction temperature is 450°C. The pressure of the gas collecting chamber is 0.2 MPa. After the oil and gas come out of the riser, they are separated by the cyclone separator and then enter the fractionation system at the rear. The spent catalyst with carbon enters the stripping section, the spent catalyst after the stripping goes to the regenerator for regeneration, a...
Embodiment 2
[0052] The test was carried out using the same riser reactor as in Example 1 above. The raw oil used was the same as that in the above example. The test steps and methods were exactly the same as in the example, except that the catalyst used was changed from the conventional particle size catalyst A of Example 1 to Coarse particle size catalyst B. The test conditions and test results are listed in Table 3, and the diesel properties are listed in Table 4.
[0053] It can be seen from Table 3 that the diesel yield of this embodiment is as high as 46.15 wt%; from Table 4, it can be seen that the diesel cetane number of this embodiment is as high as 52, and the diesel cetane number barrel is as high as 2399.8.
[0054] It can also be seen from Table 3 that the yield of dry gas and coke in this example is significantly lower than that in Example 1, indicating that the cracking catalyst B with coarse particle size can reduce the yield of dry gas and coke more than the cracking catalyst A...
PUM
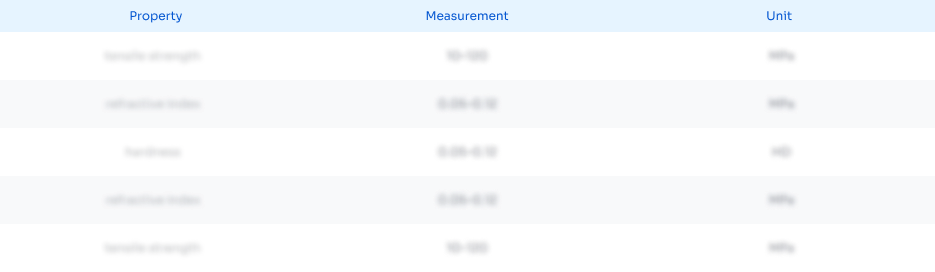
Abstract
Description
Claims
Application Information

- R&D
- Intellectual Property
- Life Sciences
- Materials
- Tech Scout
- Unparalleled Data Quality
- Higher Quality Content
- 60% Fewer Hallucinations
Browse by: Latest US Patents, China's latest patents, Technical Efficacy Thesaurus, Application Domain, Technology Topic, Popular Technical Reports.
© 2025 PatSnap. All rights reserved.Legal|Privacy policy|Modern Slavery Act Transparency Statement|Sitemap|About US| Contact US: help@patsnap.com