Method for synthesizing polyethoxylated derivative
A technology of polyethoxylation and synthesis method, which is applied in chemical instruments and methods, preparation of organic compounds, organic chemistry, etc., can solve the problems of reduced reaction conversion rate, application limitation, and increased production cost, and shortens the reaction time. , Improve product purity, strengthen the effect of stripping effect
- Summary
- Abstract
- Description
- Claims
- Application Information
AI Technical Summary
Problems solved by technology
Method used
Image
Examples
Embodiment 1
[0038] Preparation of FA-3EO (fatty alcohol polyoxyethylene ether):
[0039] 1. Pre-reactor:
[0040] 1.1 The initial pressure is -0.5kg / cm 2 Add C to the prereactor of g 12 -C 14 Fatty alcohol (FA, average molecular weight=194) 7138kg and 48wt% KOH solution 20.8kg reaction;
[0041] 1.2 Vacuum the pre-reactor to reduce the pressure in the reactor to -0.952kg / cm 2 g, to remove the 12 -C 14 The fatty alcohol and KOH solution are brought into the water in the prereactor. The operating temperature of pre-reactor vacuuming is 125°C, and the operating time is 25 minutes;
[0042] 1.3 Raise the temperature of the catalytic product in the pre-reactor to 150°C and transport it to the main reactor through a pump;
[0043] The reaction formula of the reaction in the pre-reactor is as follows: RXH+KOH---->RX - K + +H 2 o
[0044] 2. The main reactor:
[0045] 2.1 After the catalytic product in the pre-reactor is added to the main reactor, it is circulated and sprayed through...
Embodiment 2
[0060] Preparation of NP-9EO (nonylphenol poly-9oxyethylene ether):
[0061] 1. Pre-reactor:
[0062] 1.1 The initial pressure is -0.4kg / cm 2 Add nonylphenol (NP, molecular weight=223) 4320kg and 48wt%KOH solution 20.8kg reaction in the prereactor of g;
[0063] 1.2 Vacuum the pre-reactor to reduce the pressure in the reactor to -0.8kg / cm 2 g, used to remove the water brought into the pre-reactor by nonylphenol and KOH solution. The operating temperature of pre-reactor vacuuming is 140°C, and the operating time is 30 minutes;
[0064] 1.3 Then raise the temperature of the catalytic product in the pre-reactor to 170°C, and pump it to the main reactor;
[0065] The reaction formula of the reaction that takes place in the prereactor is as follows:
[0066] RXH+KOH----------------->RX - K + +H 2 o
[0067] 2. The main reactor:
[0068] 2.1 After the material in the pre-reactor is added to the main reactor, it is sprayed circularly through the spray nozzle set in the main...
Embodiment 3
[0083] Preparation of PEG1000 (polyethylene glycol, average molecular weight=1000):
[0084] The production of PEG1000 is divided into two steps:
[0085] In the first step, PEG400 is produced by DEG:
[0086] 1. Pre-reactor:
[0087] 1.1 The initial pressure is -0.6kg / cm 2 Add diethylene glycol (DEG, molecular weight=106) 2544kg and 48wt% KOH solution 20.8kg reaction in the prereactor of g;
[0088] 1.2 Vacuum the pre-reactor to reduce the pressure in the reactor to -1kg / cm 2 g, used to remove the water brought into the pre-reactor by diethylene glycol and KOH solution. The operating temperature of pre-reactor vacuuming is 120°C, and the operating time is 25 minutes;
[0089] 1.3 Raise the temperature of the catalytic product in the pre-reactor to 150°C and transport it to the main reactor through a pump;
[0090]The reaction formula of the reaction that takes place in the prereactor is as follows:
[0091] R(XH) 2 +2KOH ------------>RX 2- (K + ) 2 +2H 2 o
[009...
PUM
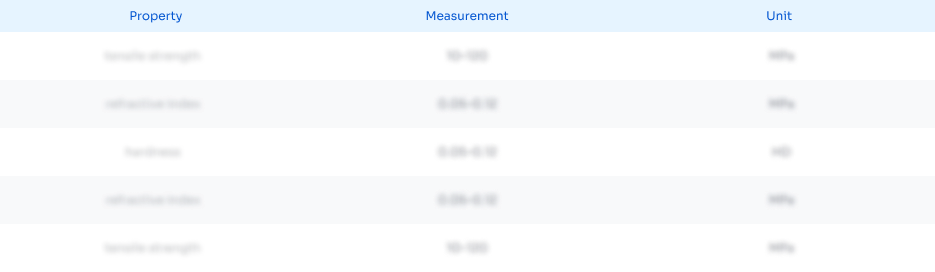
Abstract
Description
Claims
Application Information

- R&D
- Intellectual Property
- Life Sciences
- Materials
- Tech Scout
- Unparalleled Data Quality
- Higher Quality Content
- 60% Fewer Hallucinations
Browse by: Latest US Patents, China's latest patents, Technical Efficacy Thesaurus, Application Domain, Technology Topic, Popular Technical Reports.
© 2025 PatSnap. All rights reserved.Legal|Privacy policy|Modern Slavery Act Transparency Statement|Sitemap|About US| Contact US: help@patsnap.com