Method for preparing chlorinated butyl rubber damping material
A technology of chlorinated butyl rubber and damping material, applied in the field of rubber damping material, can solve the problems of limitation and low vibration damping performance, and achieve the effect of improving performance, improving strength and wide application range
- Summary
- Abstract
- Description
- Claims
- Application Information
AI Technical Summary
Problems solved by technology
Method used
Image
Examples
preparation example Construction
[0020] The invention provides a kind of preparation method of chlorinated butyl rubber damping material, comprises the following steps:
[0021] Mixing chlorinated butyl rubber, C5 / C9 copolymerized petroleum resin, filler, zinc oxide, 2,2-dithiobenzothiazole and tetramethylthiuram disulfide to obtain a rubber compound, the butyl chloride The mass ratio of the base rubber to the C5 / C9 copolymerized petroleum resin is 75-85: 15-25;
[0022] The rubber material is vulcanized to obtain a chlorinated butyl rubber damping material.
[0023] The invention prepares the chlorinated butyl rubber damping material by blending the chlorinated butyl rubber and C5 / C9 copolymerized petroleum resin, and the temperature range of the effective damping function zone of the obtained damping material is -40 DEG C to 40 DEG C, and the application range is relatively wide.
[0024] In the invention, firstly, chlorinated butyl rubber, C5 / C9 copolymerized petroleum resin, filler, zinc oxide, 2,2-dithi...
Embodiment 1
[0036] Put 75 grams of chlorinated butyl rubber and 15 grams of C5 / C9 copolymerized petroleum resin into the internal mixer, knead for 3 to 5 minutes, then add 15 grams of white carbon black, knead for 3 to 5 minutes, and then put 3 grams of zinc oxide, 0.5 grams of 2,2-dithiobenzothiazole and 0.4 grams of tetramethylthiuram disulfide were mixed for 3 to 5 minutes to obtain a rubber compound. Preheat a 1 mm thick mold in a flat vulcanizer at 156°C for 30 minutes, then put the rubber into the mold and vulcanize at 156°C and 12MPa for 30 minutes to obtain chlorobutyl rubber and C5 / C9 Copolymerized petroleum resin damping rubber sheet.
[0037] The damping rubber sheet is analyzed by a damping analyzer, and the results can be found in figure 1 , figure 1 The damping spectrum of the chlorinated butyl rubber damping material provided in the examples and comparative examples of the present invention, wherein, curve a is the damping spectrum of the chlorinated butyl rubber damping...
Embodiment 2
[0039] Put 85 grams of chlorinated butyl rubber and 25 grams of C5 / C9 copolymerized petroleum resin into an internal mixer, knead for 3 to 5 minutes, then add 20 grams of white carbon black, knead for 3 to 5 minutes, and then put 5 g of zinc oxide, 1 g of 2,2-dithiobenzothiazole, and 0.6 g of tetramethylthiuram disulfide were mixed for 3 to 5 minutes to obtain a rubber compound. Preheat a 1 mm thick mold in a flat vulcanizer at 160°C for 30 minutes, then put the rubber into the mold and vulcanize at 160°C and 15MPa for 30 minutes to obtain chlorobutyl rubber and C5 / C9 Copolymerized petroleum resin damping rubber sheet.
[0040] The damping rubber sheet is analyzed by a damping analyzer, and the results can be found in figure 1 , figure 1 The damping spectrum of the chlorinated butyl rubber damping material provided in the examples and comparative examples of the present invention, wherein, curve b is the damping spectrum of the chlorinated butyl rubber damping material prov...
PUM
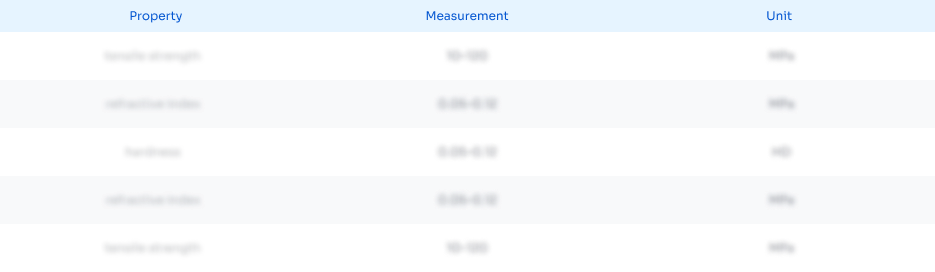
Abstract
Description
Claims
Application Information

- Generate Ideas
- Intellectual Property
- Life Sciences
- Materials
- Tech Scout
- Unparalleled Data Quality
- Higher Quality Content
- 60% Fewer Hallucinations
Browse by: Latest US Patents, China's latest patents, Technical Efficacy Thesaurus, Application Domain, Technology Topic, Popular Technical Reports.
© 2025 PatSnap. All rights reserved.Legal|Privacy policy|Modern Slavery Act Transparency Statement|Sitemap|About US| Contact US: help@patsnap.com