Self-cyclic utilization device for sinter machine tail smoke and tail wind box smoke
A sintering machine and self-circulation technology, applied in the sintering field, can solve the problems of increased equipment cost, rapid cooling, high pressure, etc., and achieve the effects of improving quality and yield, reducing rapid cooling pulverization, and reducing air leakage rate
- Summary
- Abstract
- Description
- Claims
- Application Information
AI Technical Summary
Problems solved by technology
Method used
Image
Examples
Embodiment Construction
[0019] see figure 2 , the present invention relates to a device for self-circulation utilization of sintering machine tail gas and machine tail wind box flue gas, which includes a trolley 1, the tail of the trolley 1 is provided with a dust removal cover 9, and the upper part of the dust removal cover 9 is canceled The original tail dust removal vent is changed to a closed structure, and the lower part is provided with a single-toothed roller 7 for crushing the sintered material. A sealing cover 8 is added on the top of the rear 40%~60% section of the trolley 1, and a partition II 11 is arranged inside the sealing cover 8, and the partition II 11 separates the sealing cover 8 into two sections before and after. The airtight front section of the sealing cover 8 forms a negative pressure that communicates with the end of the large flue machine tail, and the rear section of the sealing cover 8 communicates with the dust removal cover 9 at the machine tail. A plurality of bellow...
PUM
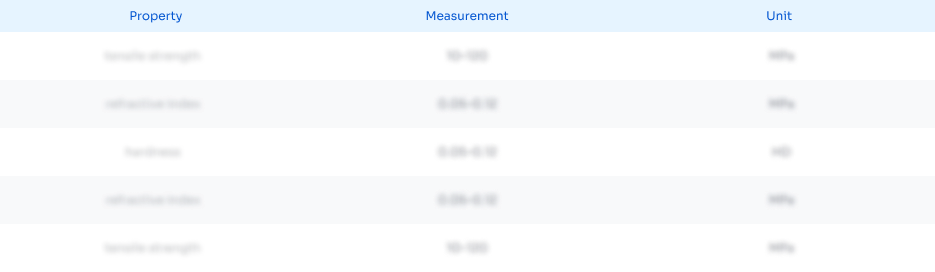
Abstract
Description
Claims
Application Information

- Generate Ideas
- Intellectual Property
- Life Sciences
- Materials
- Tech Scout
- Unparalleled Data Quality
- Higher Quality Content
- 60% Fewer Hallucinations
Browse by: Latest US Patents, China's latest patents, Technical Efficacy Thesaurus, Application Domain, Technology Topic, Popular Technical Reports.
© 2025 PatSnap. All rights reserved.Legal|Privacy policy|Modern Slavery Act Transparency Statement|Sitemap|About US| Contact US: help@patsnap.com