Inverter module for controlling brushless direct current (DC) motor
A technology of DC motor and inverter module, which is applied in the direction of converting AC power input to DC power output, electrical components, electronic commutators, etc., which can solve the problems of increased complexity of the control system and high overall cost, etc., to achieve improved dynamics And static index, the effect of high capacity index and low cost
- Summary
- Abstract
- Description
- Claims
- Application Information
AI Technical Summary
Problems solved by technology
Method used
Image
Examples
Embodiment Construction
[0043] In a preferred embodiment of the present invention, a servo control system of a three-phase square wave brushless permanent magnet DC motor is provided, the principle of which is as follows figure 1 shown. It can be seen from the figure that the control system includes a three-phase bridge inverter circuit 101, a current sensor 102 connected to the inverter bridge, a current converter 112 that converts the sensing signal of the current sensor, and a current regulator connected in sequence Device 108, PWM modulation circuit 103, and pre-driver circuit 107. Wherein, the three-phase bridge inverter circuit 101 outputs working power to the three-phase square wave brushless permanent magnet DC motor 105 . The current converter outputs sensing signals from the linear Hall element 106 .
[0044] Such as figure 2 As shown, in a preferred embodiment of the present invention, the current sensor includes three sampling coils L1, L2, and L3 with the same number of turns, and th...
PUM
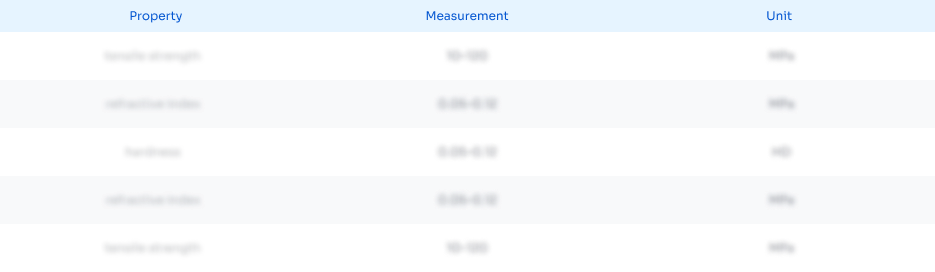
Abstract
Description
Claims
Application Information

- R&D Engineer
- R&D Manager
- IP Professional
- Industry Leading Data Capabilities
- Powerful AI technology
- Patent DNA Extraction
Browse by: Latest US Patents, China's latest patents, Technical Efficacy Thesaurus, Application Domain, Technology Topic, Popular Technical Reports.
© 2024 PatSnap. All rights reserved.Legal|Privacy policy|Modern Slavery Act Transparency Statement|Sitemap|About US| Contact US: help@patsnap.com