Chip friction clutch
A technology of friction clutches and clutches, applied in the field of clutches, can solve problems such as waste, rotten threads, high material and processing costs, and achieve the effects of reducing processing costs, improving sealing effects, and reducing material costs
- Summary
- Abstract
- Description
- Claims
- Application Information
AI Technical Summary
Problems solved by technology
Method used
Image
Examples
Embodiment Construction
[0022] see Figure 1 to Figure 5 In an embodiment of the disc friction clutch of the present invention, the axial end wall of the cover cavity of the clutch housing 1 has an extension 1a extending axially into the cavity, and a central through hole 11 is set at the center of the extension 1a. A driving disk 3 is fixed and assembled in the housing cavity in the circumferential direction, the driving disk 3 is fixed to the end surface of the outer cover 1, and is fastened and connected from the end surface by a plurality of screws 8, and the driving disk 3 is used for splined connection with the rotating shaft 6 for power transmission. The driving disc 3 is relatively rotatably covered with a driven disc combination 4, the friction pair combination 2 of the clutch is assembled between the driven disc combination and the outer cover 1, and the driven disc combination 4 meshes with a transmission gear 5 located outside the outer cover 1, The transmission gear 5 is loosely fitted o...
PUM
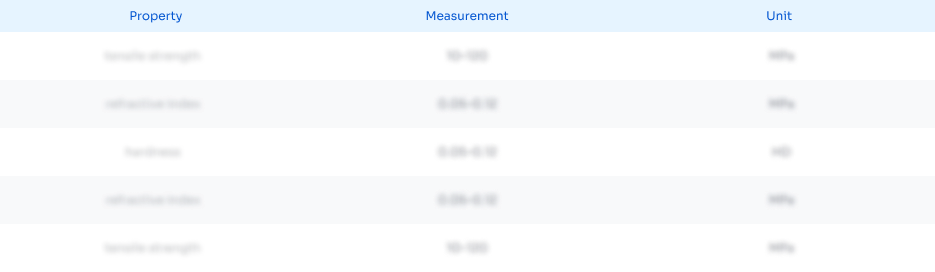
Abstract
Description
Claims
Application Information

- R&D
- Intellectual Property
- Life Sciences
- Materials
- Tech Scout
- Unparalleled Data Quality
- Higher Quality Content
- 60% Fewer Hallucinations
Browse by: Latest US Patents, China's latest patents, Technical Efficacy Thesaurus, Application Domain, Technology Topic, Popular Technical Reports.
© 2025 PatSnap. All rights reserved.Legal|Privacy policy|Modern Slavery Act Transparency Statement|Sitemap|About US| Contact US: help@patsnap.com