Co-extrusion die head for extruding profiled bars with co-extrusion surface
A technology of co-extrusion die and profile material, applied in the field of co-extrusion die, can solve the problem of uneven co-extrusion layer and achieve the effect of uniform co-extrusion layer and uniform flow
- Summary
- Abstract
- Description
- Claims
- Application Information
AI Technical Summary
Problems solved by technology
Method used
Image
Examples
Embodiment Construction
[0009] Co-extrusion die head of the present invention such as figure 2 and image 3 As shown, it includes machine neck 7, transition plate 6, bracket plate 5, compression plate 4, preformed plate 3, forming plate 2 and insert 1, splitter cone 8 is integrated with transition plate 6 through connecting rib 9, and core 11 is integrated with the bracket plate 5 through the connecting rib 10, and the insert 1 is fixed on the core 11 by screws. The co-extrusion channel is set on the preformed plate, including the main channel 17, the fan-shaped runner 16, the guide groove 18 and the co-extrusion parallel section 13, and the fan-shaped runner 16 is provided with a blocking island 15 protruding into the flow channel , so that between the blocking island 15 and the co-extrusion parallel section 13, a reservoir 14 with a section wider than that of the co-extrusion parallel section 13 is formed. The co-extrusion material is extruded into the sub-runner 16 through the main channel 17, ...
PUM
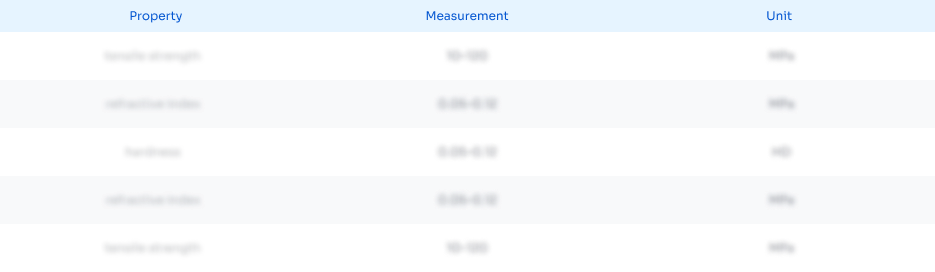
Abstract
Description
Claims
Application Information

- R&D Engineer
- R&D Manager
- IP Professional
- Industry Leading Data Capabilities
- Powerful AI technology
- Patent DNA Extraction
Browse by: Latest US Patents, China's latest patents, Technical Efficacy Thesaurus, Application Domain, Technology Topic, Popular Technical Reports.
© 2024 PatSnap. All rights reserved.Legal|Privacy policy|Modern Slavery Act Transparency Statement|Sitemap|About US| Contact US: help@patsnap.com