Method of friction welding
A friction welding and welding surface technology, which is applied in welding equipment, welding/welding/cutting items, non-electric welding equipment, etc., can solve the problems of reducing benefits and damage
- Summary
- Abstract
- Description
- Claims
- Application Information
AI Technical Summary
Problems solved by technology
Method used
Image
Examples
Embodiment Construction
[0032] Such as figure 1 As shown, fan turbine gas turbine engine 10 includes, in flow order: inlet 12 , fan section 14 , compressor section 16 , combustion section 18 , turbine section 20 , and exhaust 22 . The fan section 14 includes a fan rotor 24 carrying a plurality of circumferentially spaced radially outwardly extending fan blades 26 . Fan section 14 also includes a fan case 28 arranged coaxially with and surrounding fan rotor 24 and fan blades 26 . The fan case 28 defines a fan duct 30 . The fan case 28 is secured to the core engine case 32 by a plurality of circumferentially spaced apart and radially extending fan outlet vanes 34 .
[0033] Compressor section 16 includes one or more compressors, such as an intermediate pressure compressor (not shown) and a high pressure compressor (not shown) or a high pressure compressor (not shown). Turbine section 20 includes one or more turbines, such as a high pressure turbine (not shown), an intermediate pressure turbine (not ...
PUM
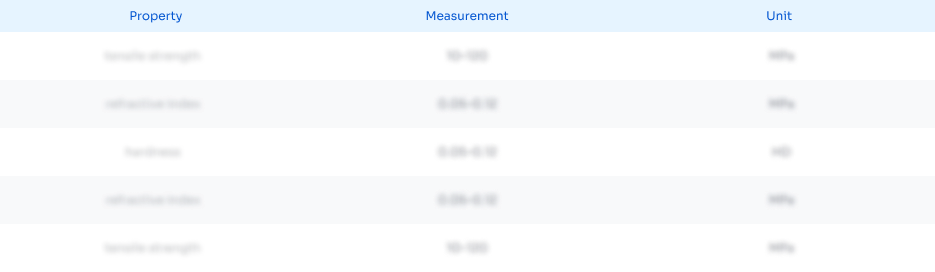
Abstract
Description
Claims
Application Information

- Generate Ideas
- Intellectual Property
- Life Sciences
- Materials
- Tech Scout
- Unparalleled Data Quality
- Higher Quality Content
- 60% Fewer Hallucinations
Browse by: Latest US Patents, China's latest patents, Technical Efficacy Thesaurus, Application Domain, Technology Topic, Popular Technical Reports.
© 2025 PatSnap. All rights reserved.Legal|Privacy policy|Modern Slavery Act Transparency Statement|Sitemap|About US| Contact US: help@patsnap.com