Compound electric arc welding method
An arc welding and arc technology, applied in arc welding equipment, welding equipment, manufacturing tools, etc., can solve the problems of high voltage arc pressure at the end of the main arc, main arc deviation, etc., and achieve improved melting speed, reliable operation, and easy operation. The effect of large-scale promotion and implementation
- Summary
- Abstract
- Description
- Claims
- Application Information
AI Technical Summary
Problems solved by technology
Method used
Image
Examples
specific Embodiment approach 1
[0017] Specific implementation mode one: the following combination figure 1 Describe this embodiment, this embodiment connects the same pole output end of main power supply 1 and auxiliary power supply 2 with the head end of main melting electrode 3 at the same time, connects the other pole output end of main power supply 1 with workpiece 4 to be welded, auxiliary The output end of the other pole of the power supply 2 is connected to the head end of the auxiliary electrode 5, and its welding method is as follows:
[0018] Put the end of the main melting electrode 3 close to the part to be welded of the workpiece 4 to be welded, so that under the action of the main power source 1, a main arc is formed between the end of the main melting electrode 3 and the surface to be welded of the workpiece 4 to be welded; at the same time, the The end of the auxiliary electrode 5 is close to the end of the main melting electrode 3, so that under the action of the auxiliary power supply 2, a...
specific Embodiment approach 2
[0020] Specific implementation mode two: the following combination figure 1 This embodiment will be described. This embodiment is a further description of Embodiment 1, and the auxiliary electrode 5 is a melting electrode or a non-melting electrode. Other components and connections are the same as those in Embodiment 1.
[0021] When the auxiliary electrode 5 is a melting electrode, the diameter of the welding wire of the auxiliary electrode 5 can be the same as that of the main melting electrode 3, or it can be different; when the auxiliary electrode 5 is a non-melting electrode, the main arc formed by the main melting electrode 3 can be used to start the arc first. , After the auxiliary electrode 5 is energized, the arc can be started automatically without high-frequency arc starting.
specific Embodiment approach 3
[0022] Specific implementation mode three: the following combination figure 2 Describe this embodiment. The difference between this embodiment and Embodiment 1 or 2 is that it also includes N additional auxiliary power sources 6 and N additional auxiliary electrodes 7, where N is a natural number greater than zero.
[0023] The homopolar output terminals of the N additional auxiliary power supplies 6 are connected to the head end of the main melting electrode 3 at the same time. The other pole output terminal of the power supply 6 is connected with the head end of an additional auxiliary electrode 7,
[0024] When implementing welding, the end of each additional auxiliary electrode 7 is approached respectively to the end of the main melting electrode 3, so that under the effect of each additional auxiliary power source 6, the end of the main melting electrode 3 is connected to the end of each additional auxiliary electrode 7. Additional auxiliary arcs are formed between them...
PUM
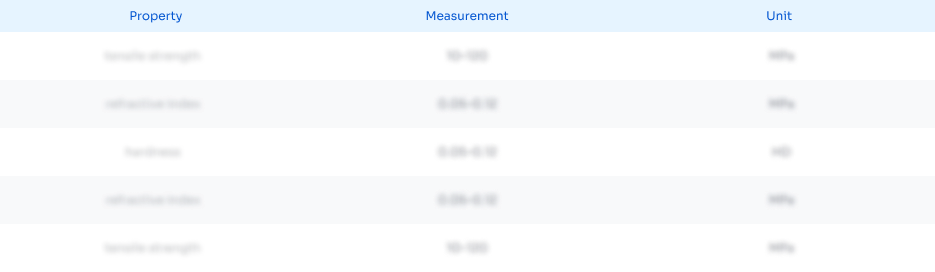
Abstract
Description
Claims
Application Information

- R&D
- Intellectual Property
- Life Sciences
- Materials
- Tech Scout
- Unparalleled Data Quality
- Higher Quality Content
- 60% Fewer Hallucinations
Browse by: Latest US Patents, China's latest patents, Technical Efficacy Thesaurus, Application Domain, Technology Topic, Popular Technical Reports.
© 2025 PatSnap. All rights reserved.Legal|Privacy policy|Modern Slavery Act Transparency Statement|Sitemap|About US| Contact US: help@patsnap.com