Metal formed die gravity tilt casting process of aluminum alloy cylinder cover
A casting process and metal mold technology, applied in the field of aluminum alloy casting, can solve the problems of difficult casting, uneven wall thickness, easy slag inclusion, etc., and achieve the effects of low casting cost, high production efficiency and fast production cycle.
- Summary
- Abstract
- Description
- Claims
- Application Information
AI Technical Summary
Problems solved by technology
Method used
Image
Examples
Embodiment Construction
[0011] The metal mold gravity tilting casting process of the aluminum alloy cylinder head of the present invention is: first, according to the sand core decomposition manufacturing process, the water jacket chamber, the air passage chamber and the oil chamber of the aluminum alloy cylinder head are made into several sand cores, and then The sand core is placed into the metal mold (that is, the core process, such as figure 1 shown), and press the riser sand core through the compression mechanism of the mold (incline) on both sides (that is, the process of pressing the riser core, such as figure 1 shown) to prevent the riser sand core from shifting during the tilting process; then, tilt the metal mold to 90 degrees so that the filter port of the sprue cup is facing upwards (such as figure 2 shown), then pour the molten aluminum into the filter port (and the filter screen) and enter the sprue cup, and then through the speed control of the first slow, then fast, and finally slow ...
PUM
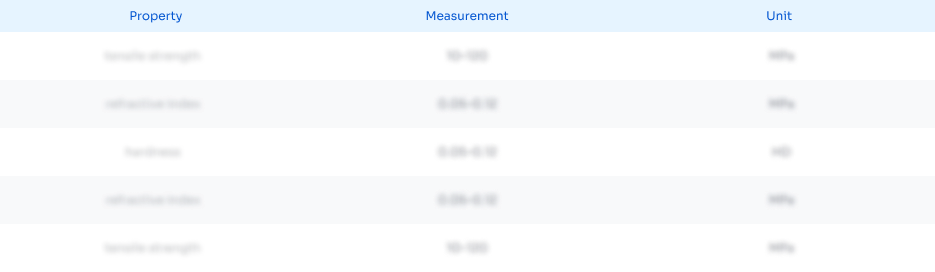
Abstract
Description
Claims
Application Information

- R&D
- Intellectual Property
- Life Sciences
- Materials
- Tech Scout
- Unparalleled Data Quality
- Higher Quality Content
- 60% Fewer Hallucinations
Browse by: Latest US Patents, China's latest patents, Technical Efficacy Thesaurus, Application Domain, Technology Topic, Popular Technical Reports.
© 2025 PatSnap. All rights reserved.Legal|Privacy policy|Modern Slavery Act Transparency Statement|Sitemap|About US| Contact US: help@patsnap.com