Actuator part inner bore combined seal ring component shaping method
A combined seal and actuator technology, applied in the direction of assembly machines, metal processing equipment, manufacturing tools, etc., can solve the problems of seal ring damage, seal damage, and low product assembly survival rate, so as to improve the survival rate and eliminate residual The effect of deformation
- Summary
- Abstract
- Description
- Claims
- Application Information
AI Technical Summary
Problems solved by technology
Method used
Image
Examples
Embodiment 1
[0010] Embodiment 1, shaping the separation bush combined sealing ring assembly. Install the separation bush sealing ring assembly 2 with the fluoroplastic sealing ring into the sealing groove of the inner hole of the separation bush 1 to form the separation bush assembly, and then insert the separation bush shaping mandrel 3 into the inner hole of the separation bush assembly , put the separator liner assembly into an oven, raise the temperature to 65°C, take it out after keeping it warm for 2 hours, and let it cool down to room temperature naturally. After assembly, the sealing performance is good.
Embodiment 2
[0011] Embodiment 2, shaping the separation bush combined sealing ring assembly. Install the separation bush sealing ring assembly 2 with the fluoroplastic sealing ring into the sealing groove of the inner hole of the separation bush 1 to form the separation bush assembly, and then insert the separation bush shaping mandrel 3 into the inner hole of the separation bush assembly , Put the separator liner assembly into an oven, raise the temperature to 70°C, take it out after keeping it warm for 1.5 hours, and let it cool down to room temperature naturally. After assembly, the sealing performance is good.
Embodiment 3
[0012] Embodiment 3, shaping the combined sealing ring assembly of the main piston. Install the main piston seal ring assembly 5 with the fluoroplastic sealing ring in the sealing groove of the inner hole of the main piston 4 to form the main piston assembly, then insert the main piston shaping mandrel 6 into the inner hole of the main piston assembly, and place the main piston assembly Put it in an oven, raise the temperature to 75°C, keep it warm for 1 hour, take it out, and let it cool down to room temperature naturally. After assembly, the sealing performance is good.
PUM
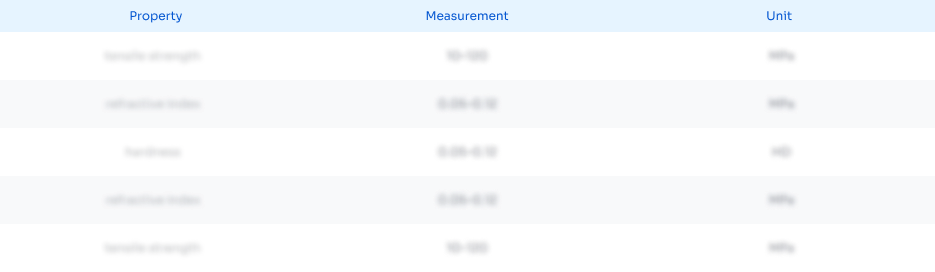
Abstract
Description
Claims
Application Information

- Generate Ideas
- Intellectual Property
- Life Sciences
- Materials
- Tech Scout
- Unparalleled Data Quality
- Higher Quality Content
- 60% Fewer Hallucinations
Browse by: Latest US Patents, China's latest patents, Technical Efficacy Thesaurus, Application Domain, Technology Topic, Popular Technical Reports.
© 2025 PatSnap. All rights reserved.Legal|Privacy policy|Modern Slavery Act Transparency Statement|Sitemap|About US| Contact US: help@patsnap.com