Preparation method of adipic acid-di-n-propyl ester
A technology of di-n-propyl adipate and adipic acid, applied in the field of preparation of di-n-propyl adipate, can solve the problems of unfavorable economic benefits, difficulty in cost reduction, low production efficiency, etc. The effect of production cost and convenient operation
- Summary
- Abstract
- Description
- Claims
- Application Information
AI Technical Summary
Problems solved by technology
Method used
Examples
preparation example Construction
[0018] A preparation method of di-n-propyl adipate, comprising the following steps:
[0019] (1) Esterification step: drop into 100 kilograms of adipic acid, 85 kilograms of n-propanols, 0.3 kilograms of concentrated sulfuric acid successively in a 300-liter reactor with heating device, electric stirring, thermometer water circulation condenser and oil-water separator , heated to boiling reaction while stirring, kept boiling reflux state, continuously separated water from the oil-water separator, until no water was generated, stopped heating, and the esterification reaction was terminated.
[0020] (2) Water washing step: add 50 kilograms of water to the mixed solution obtained after the esterification reaction, stir evenly, leave to stand for stratification, and remove the water layer therein.
[0021] (3) Refining step: add 0.5 kg of refining agent (calcium hydroxide, magnesium hydroxide, activated carbon, magnesium sulfate mixture, its weight ratio 1:1:2:1.5) to the mixed s...
Embodiment 2
[0024] A preparation method of di-n-propyl adipate, comprising the following steps:
[0025] (1) Esterification step: drop into 100 kilograms of adipic acid, 85 kilograms of n-propanols, 0.3 kilograms of concentrated sulfuric acid successively in a 300-liter reactor with heating device, electric stirring, thermometer water circulation condenser and oil-water separator , heated to boiling reaction while stirring, kept boiling reflux state, continuously separated water from the oil-water separator, until no water was generated, stopped heating, and the esterification reaction was terminated.
[0026] (2) Water washing step: add 50 kilograms of water to the mixed solution obtained after the esterification reaction, stir evenly, leave to stand for stratification, and remove the water layer therein.
[0027] (3) Refining step: add 0.6 kg of refining agent (calcium hydroxide, magnesium hydroxide, gac, magnesium sulfate mixture, its weight ratio 1:1:2:1.5) to the mixed solution after...
Embodiment 3
[0030] A preparation method of di-n-propyl adipate, comprising the following steps:
[0031] (1) Esterification step: drop into 100 kilograms of adipic acid, 85 kilograms of n-propanols, 0.3 kilograms of concentrated sulfuric acid successively in a 300-liter reactor with heating device, electric stirring, thermometer water circulation condenser and oil-water separator , heated to boiling reaction while stirring, kept boiling reflux state, continuously separated water from the oil-water separator, until no water was generated, stopped heating, and the esterification reaction was terminated.
[0032] (2) Water washing step: add 50 kilograms of water to the mixed solution obtained after the esterification reaction, stir evenly, leave to stand for stratification, and remove the water layer therein.
[0033] (3) Refining step: add 0.7 kg of refining agent (calcium hydroxide, magnesium hydroxide, activated carbon, magnesium sulfate mixture, its weight ratio 1:1:2:1.5) to the mixed s...
PUM
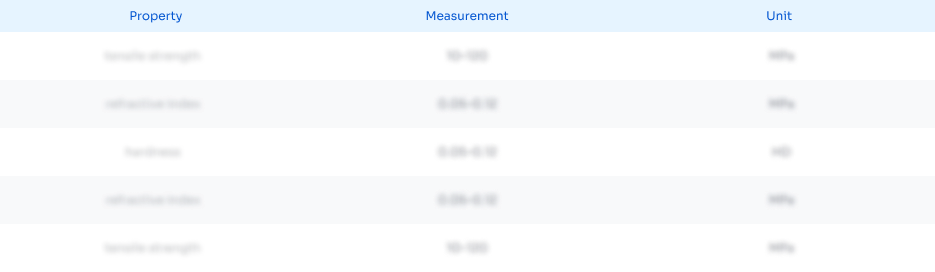
Abstract
Description
Claims
Application Information

- R&D Engineer
- R&D Manager
- IP Professional
- Industry Leading Data Capabilities
- Powerful AI technology
- Patent DNA Extraction
Browse by: Latest US Patents, China's latest patents, Technical Efficacy Thesaurus, Application Domain, Technology Topic, Popular Technical Reports.
© 2024 PatSnap. All rights reserved.Legal|Privacy policy|Modern Slavery Act Transparency Statement|Sitemap|About US| Contact US: help@patsnap.com