Etching device and method
An etching device and etching technology are applied in the direction of electrical components, semiconductor/solid-state device manufacturing, circuits, etc., which can solve the problems of uneven etching and inaccurate etching rate control, etc., and achieve the effect of precise control
- Summary
- Abstract
- Description
- Claims
- Application Information
AI Technical Summary
Problems solved by technology
Method used
Image
Examples
Embodiment approach
[0017] Based on this, the present invention provides an etching device. According to one embodiment, the etching device includes a cavity with a plurality of air inlets, and a wafer tray is provided in the cavity for carrying a wafer. The cavity also includes a plurality of etching control units located under the wafer tray, and the etching control units are used to control the voltage of the corresponding wafer to be etched, and the polarity of the voltage is the same as that passed into the cavity through the air inlet. The polarity of the charged etching gas is opposite.
[0018] In the embodiment of the above etching device, the etching control unit applies a voltage opposite in polarity to the charged etching gas at the corresponding position of the wafer to be etched, and forms a corresponding electric field at the position to be etched. Due to the principle of attraction of opposites, the etching gas will be adsorbed at the position of the wafer to be etched, thereby pe...
PUM
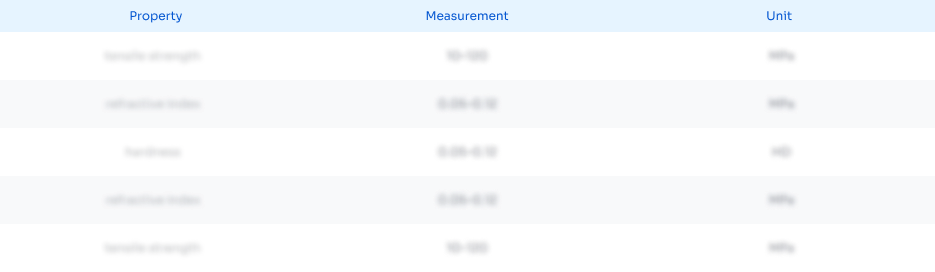
Abstract
Description
Claims
Application Information

- R&D
- Intellectual Property
- Life Sciences
- Materials
- Tech Scout
- Unparalleled Data Quality
- Higher Quality Content
- 60% Fewer Hallucinations
Browse by: Latest US Patents, China's latest patents, Technical Efficacy Thesaurus, Application Domain, Technology Topic, Popular Technical Reports.
© 2025 PatSnap. All rights reserved.Legal|Privacy policy|Modern Slavery Act Transparency Statement|Sitemap|About US| Contact US: help@patsnap.com