Process for removing heavy metal from sludge of sewage treatment plants
A technology for heavy metals and sewage treatment plants, which is used in sewage/sludge fertilizer, sludge treatment, biological sludge treatment, etc. It can solve the problems of difficulty in ensuring the removal stability of heavy metals, long extraction period of a single microorganism, and single type of leached heavy metals. , to achieve the effect of saving sludge dewatering costs, saving secondary construction costs, and improving sludge dewatering performance
- Summary
- Abstract
- Description
- Claims
- Application Information
AI Technical Summary
Problems solved by technology
Method used
Image
Examples
Embodiment 1
[0015] (1) Biological leaching treatment: transform the sludge aerobic digestion tank of the sewage treatment plant into a biological leaching tank through anticorrosion, add elemental sulfur 0.5-30g / L sludge into the tank, and inoculate the mass ratio of 1% respectively -5% Thiobacillus and 1%-3% acidophilic mold, carry out aeration and leaching for 2-6 days; until the pH value is less than 2. At this time, the heavy metal dissolution rate reaches the standard;
[0016] (2) Plate-and-frame filter press separation: use a pump to pump the sludge and water phase after biological leaching into the first plate-and-frame filter press for filter press separation, and obtain sludge from which heavy metals have been removed and sewage containing heavy metals ; Sewage containing heavy metals enters the waste liquid recovery tank;
[0017] (3) After the heavy metal-removed sludge is neutralized with alkaline substances, it is transported to the sludge composting plant for composting; ...
Embodiment 2
[0020] The difference from Example 1 is that the bioleaching tank of this example is a facility transformed from an aerobic digester.
Embodiment 3
[0022] The difference from Example 1 is that the bioleaching tank of this example is transformed from an anaerobic digester through anti-corrosion and adding an aeration device.
PUM
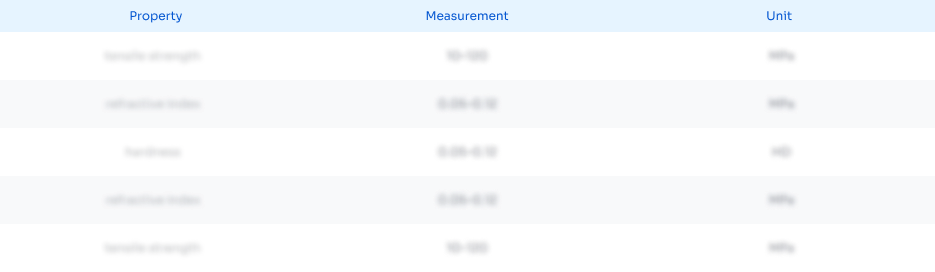
Abstract
Description
Claims
Application Information

- Generate Ideas
- Intellectual Property
- Life Sciences
- Materials
- Tech Scout
- Unparalleled Data Quality
- Higher Quality Content
- 60% Fewer Hallucinations
Browse by: Latest US Patents, China's latest patents, Technical Efficacy Thesaurus, Application Domain, Technology Topic, Popular Technical Reports.
© 2025 PatSnap. All rights reserved.Legal|Privacy policy|Modern Slavery Act Transparency Statement|Sitemap|About US| Contact US: help@patsnap.com